10 Best Transloading Equipment & Solutions for Efficient Logistics in 2024
Searching for the latest transloading equipment?
One of the biggest transloading challenges you’ll face is inefficient processes.
When you don’t use the right transloading equipment, loading and unloading slow down because of iterative and manually-driven operations.
A survey by WSL revealed that 63% of logistics businesses aim to upgrade their equipment. The primary motivation is to streamline effort-intensive, manual tasks.
If you’re looking to invest in revolutionary transloading equipment, I’ve rounded up the latest technologies that you should consider. These tools can help streamline your transloading process to improve worker throughput and profits for your transload yard.
They’ll also help you to optimize your transloading operations to enhance worker safety and increase regulatory compliance when you’re handling dangerous cargo goods.
If you’d like to diversify your logistics expertise and strategies, check out this article I wrote about rail to truck transloading and its cost-benefits.
In this article, we’ll discuss game-changing transloading equipment solutions for efficient logistics in 2024 to help improve your transloading and shipping operations.
Let’s get started.
1. Barcode scanners
Inventory management can be very challenging.
However, it is an essential part of the job because you may need to store goods in your transloading warehouse temporarily in readiness for packaging, palletization or pickup.
When inventory record taking is poor, inventory errors will grow rampant, which might make inventory processing take a very long time to complete.
A survey by DC Velocity indicated that 77% of businesses prioritize barcoding as an important inventory management feature when buying warehouse transloading tools & software. That’s because it can cut down on inventory errors and hasten processing.
With fewer errors, this can mean more accurate order fulfillment and fewer reverse logistics for your business.
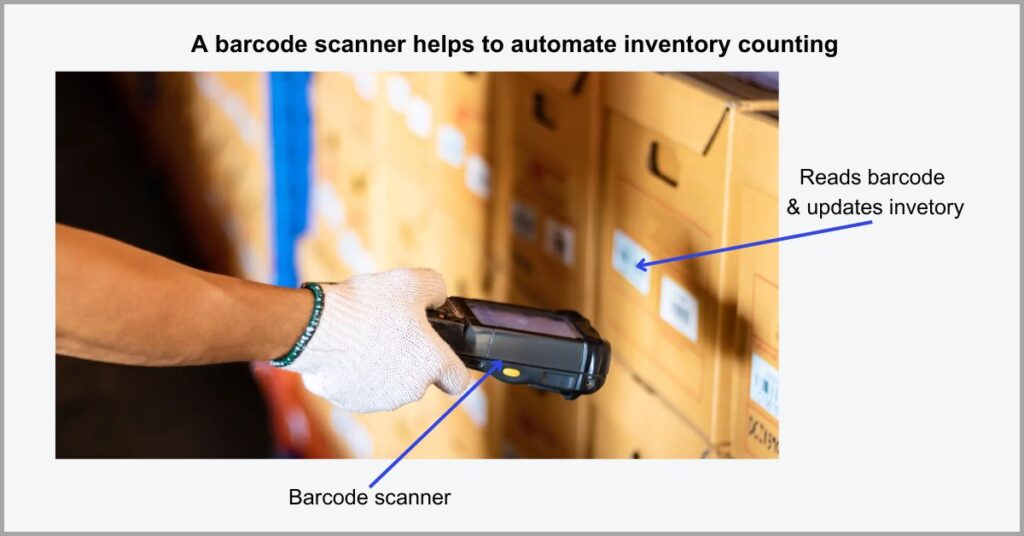
So how do barcode inventory scanners work?
Well, each pallet or freight is branded with a barcode label. You can then scan this label with a handheld scanner, which is often connected to a transload warehouse management system that automatically updates inventory counts.
If you need a great transload management software to pair up with modern barcode scanners, our maintenance-free solution is a great option.
Click here to start your free transloads.co trial to enhance inventory tracking.
With our software, you can leverage barcode scanning technology to improve efficiency, and worker productivity. You also get end-to-end inventory tracking for commodities in railcars and warehouses to improve inventory visibility for your transload yard.
2. Palletizers
So what does a palletizer do during transloading?
It’s a machine that automatically stacks goods onto a pallet, and overall enables the efficient palletization of goods to improve handling and cut out space wastage.
Without palletizers, you may need to move commodities as loose freight, which is a very time and effort-intensive affair that also raises the risk of worker injury.
A survey by Logistics Management showed that 72% of shippers palletize corrugated boxes. When quizzed why, they said palletizing goods was necessary to speed up handling and reduce storage space.
This survey also revealed that other common commodities that facilities often palletize include bags, drums, pails and reusable plastic containers (RPCs).
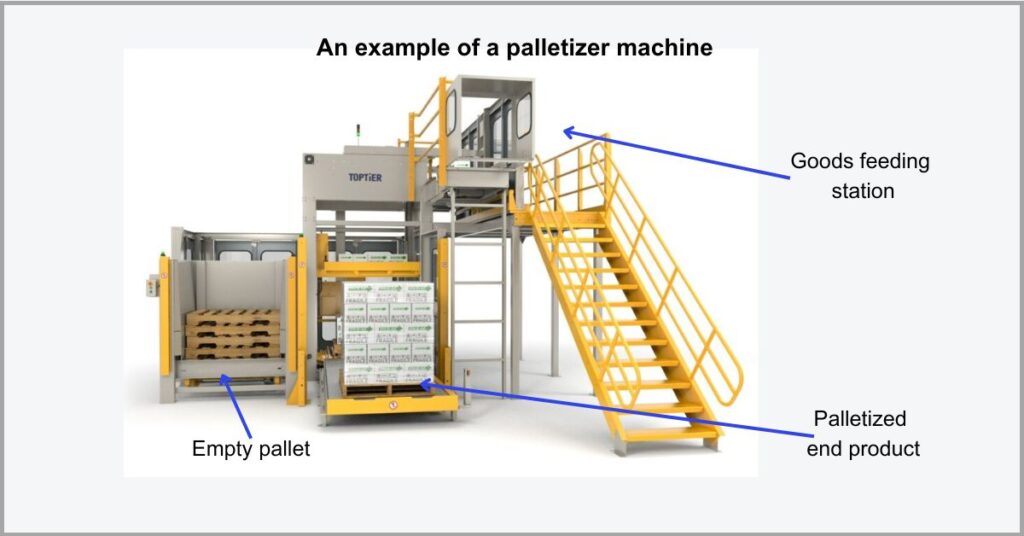
Palletization is often carried out for identical items.
For example, if you need to transload and ship drums of vegetable oil, palletization is a great way to bundle these items onto a single pallet for more efficient loading.
A palletizer machine can help you automate this process, enabling high precision and high-speed palletizing of goods. It’s one of the tech innovations in logistics that’s taken the transloading world by storm due to huge productivity benefits.
One example of an excellent palletizer machine is the HL4200 high level palletizer.
This transloading equipment is connected to a conveyor that moves items to an automatic sorter, which rearranges and palletizes commodities at high speeds.
3. Forklift trucks
Transloading can involve lifting heavy cargo.
This may include palletized or even bulky goods that may not be suitable for palletization including refrigerators and construction items like iron girders, for example.
Overall, heavy loads that require a great amount of effort to lift and transload can easily stall your transloading processes and reduce worker productivity.
A survey by Newcastle Systems revealed that 25% of warehouse workers said the physically demanding nature of the job is the top struggle. In particular, they find it very challenging to move heavy loads all day.
Transloading equipment such as forklifts make the work much lighter, enabling you to move loads more effortlessly.
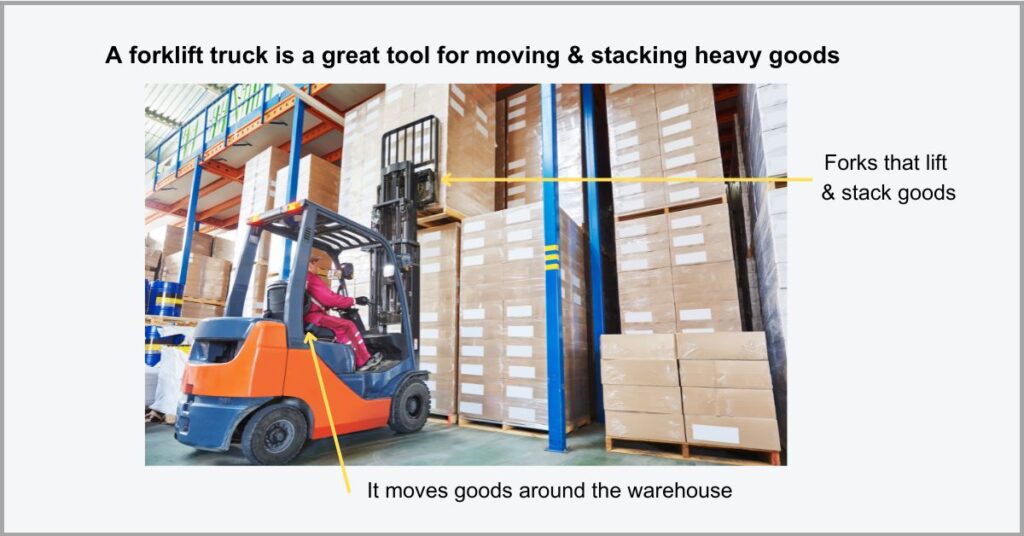
But how do forklift trucks improve your transloading operations?
For one, these offer a higher load capacity than the average worker, enabling you to move larger quantities of goods during cargo transfers. This means that you can decrease turnaround time during transloading to speed up shipping.
This equipment also solves other main transloading challenges such as the physical fatigue of warehouse workers. It does this by taking over heavy load lifting that can greatly increase the strain on dock workers and transload operators.
By easing the physically demanding nature of the job and making work lighter for your staff, forklift trucks therefore positively influence transload worker satisfaction.
4. Transload pumps
Need to transload liquid bulk materials?
Your facility may receive special requests to transload liquid bulk commodities such as crude oil and liquified natural gas. These attract unique handling needs and safety concerns because of being highly flammable goods.
For instance, when handling dangerous liquid bulk goods like butane, there’s a high risk of gas leakages and explosions that lead to physical harm.
A survey by IATA revealed that 40% of shippers increased their dangerous goods investments in 2024. In particular, many of them plan to invest more in safer cargo handling and switching equipment.
This includes tools such as transload pumps which can help you improve worker safety and compliance.
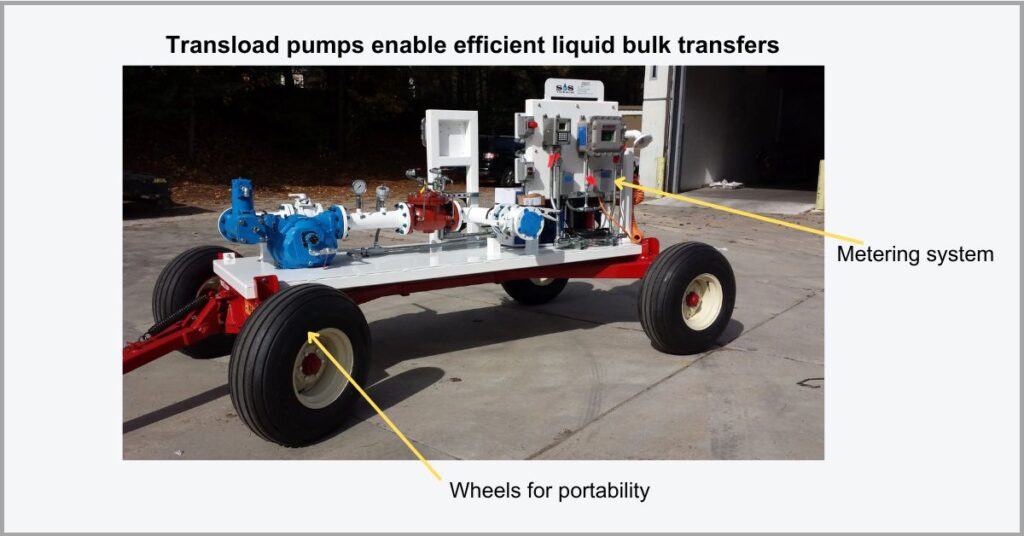
A transload pump is a transloading equipment that enables you to efficiently siphon liquid bulk materials from one vessel to another.
It is a very important tool during butane transload shipping, and when you want to transfer liquified natural gas in general. In such cases, it enables you to move the material from a rail to a truck tanker or vice versa according to your shipping needs.
Transload pumps offer very high flow rate capacity and contain safety features that enable you to track gas leakages.
Aside from butane and crude oil, other commodities that these equipment can help you transload also include milk, hydrogen peroxide, and even animal feed.
5. Reach stackers
So what is a reach stacker?
It’s basically a small vehicle that you use to lift and move very heavy intermodal containers and it’s necessary for more efficient container handling and stacking.
When container stacking is inefficient, you’ll struggle to make the most of existing floorspace thereby wasting a valuable resource for your facility.
In fact, insufficient space is a top concern for 36% of warehouses and distribution centers, according to a Statista survey. When there’s a lot of space wastage, this minimizes the amount of inventory you can hold at a time.
By limiting your storage space, inefficient container stacking therefore decreases your freight capacity, which negatively impacts your bottom line.
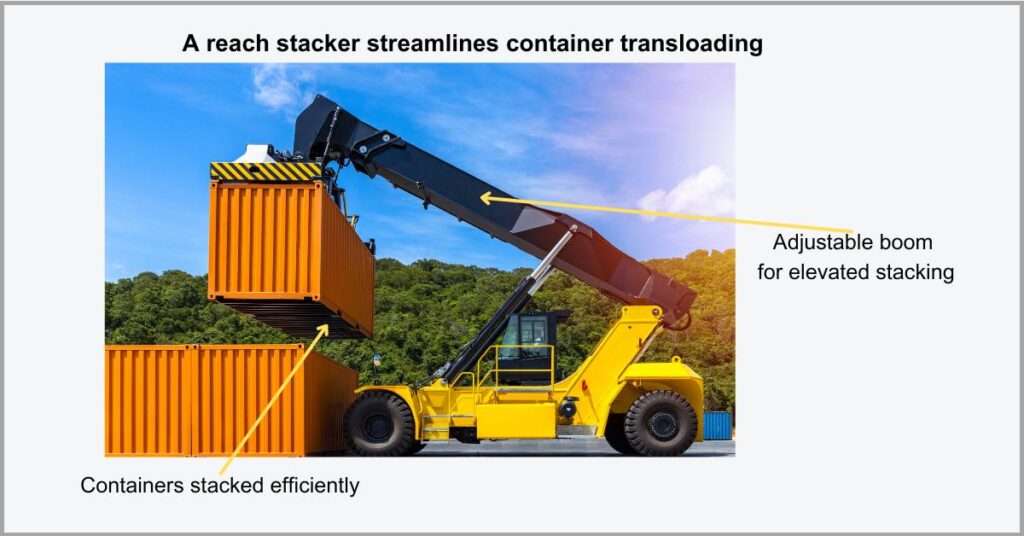
With reach stackers, you improve container handling as well as space utilization.
The vehicles are useful for transloading & intermodal shipping operations, when you’re working with intermodal containers that stay shut throughout. They can help you stack containers to very high levels to ensure efficient space utilization.
If you’d like to optimize yard space and transload operations at large, we can help.
Click here to get our premium support services, where we’ll guide you on how to improve space and operational efficiency for your facility.
With our guidance, you can upskill staff in better space utilization practices and skills and improve intermodal container transloading processes for your business.
6. Refrigerated boxcars
Cold chain commodities attract unique logistics concerns.
There’s the need to ensure that the freight and its content remains at a specified temperature even during the entire transloading process, even when you need to deconsolidate and expose the cargo to exterior temperatures.
When your cold chain handling processes are poor, cases of spoilage of perishable cargo increases, raising the risk of freight rejection by the shipper.
In fact, Statista showed that 62% of shippers ranked improper handling of goods during cold chain logistics as a top challenge. They particularly singled out temperature monitoring as the biggest obstacle because it makes it difficult to prove freight integrity.
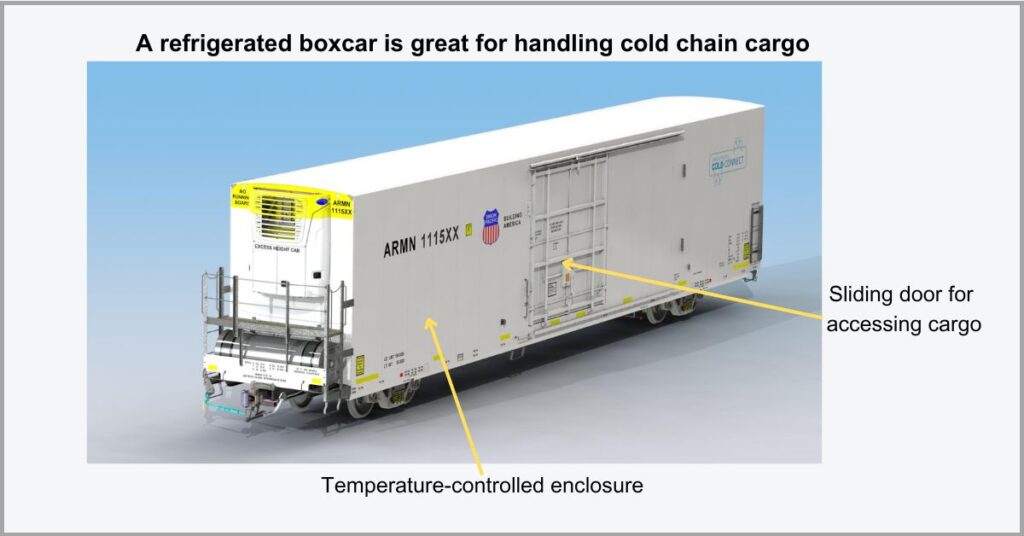
It’s important to note that refrigerated boxcars aren’t usually a property of the transload facility but the rail company itself, and they’re used at the shipper’s request.
Nonetheless, they offer temperature monitoring and regulation features that enable you to maintain the cargo at required temperatures during transloading. They also capture data that proves to shippers you handled their cargo appropriately.
So this is why they are a crucial part of effective railroad logistics, especially when you’re transloading cold chain cargo such as fresh produce and pharmaceuticals like vaccines and medicines.
When paired with railroad sidings, you can transport refrigerated boxcar freight directly to a temperature-controlled warehouse zone when you can safely load or unload goods.
7. Dock levelers
What are dock levelers and what is their purpose?
This is a transloading equipment that you typically use at a loading dock to create a level surface between the dock and the trailer you want to load or offload. It prevents dock workers from falling in between these two platforms.
That said, your loading dock is full of many workplace hazards such as ladder slips and falls which can lead to work injury, lawsuits and lower productivity.
There were 5,486 fatal workplace injuries in 2022, according to a study by the US Bureau of Labor Statistics. In transloading warehouses, a good number of these accidents took place at loading docks.
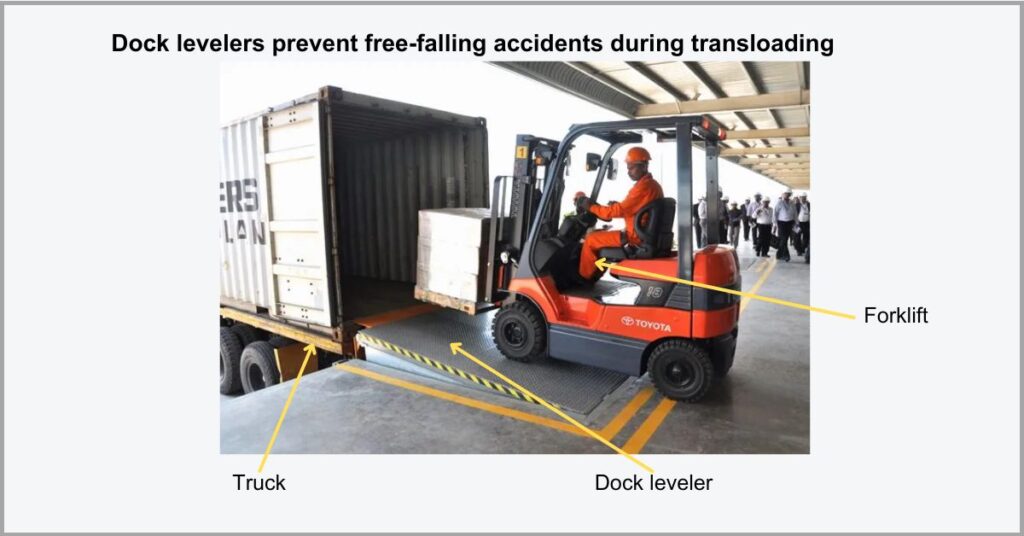
Dock levelers are a great tool for improving workplace safety.
They are more commonplace during transloading and cross docking processes, where you’ll need to move freight between two different trucks at different loading docks of your transloading facility to enable just-in-time shipping.
I recommend hydraulic dock levelers which offer added safety features that hold up the platform and prevent it from collapsing in case the trailer moves unexpectedly. In such cases, it prevents dock worker accidents resulting from free falling.
You should also consider dock levers that come with vehicle restraints. These prevent the trailer from creeping forward due to the impact of loading and unloading tasks.
8. Transloader conveyors
Transloading can also involve dry bulk goods.
This covers commodities such as fertilizer, grains and minerals and aggregates, which attract unique concerns because they’re usually unpalletized and therefore challenging to transfer due to the risk of spillage.
What’s more, transloading dry bulk commodities such as coal creates harmful pollutants and dust, which can lead to environmental compliance issues.
A study by MHI revealed that 48% of logistics businesses face increased pressure to become more eco-friendly. This pressure is coming from tightening regulatory environments that are inflicting suspensions and fines for violations.
It’s partly for this reason that your transloading facility should consider investing in transloader conveyors.
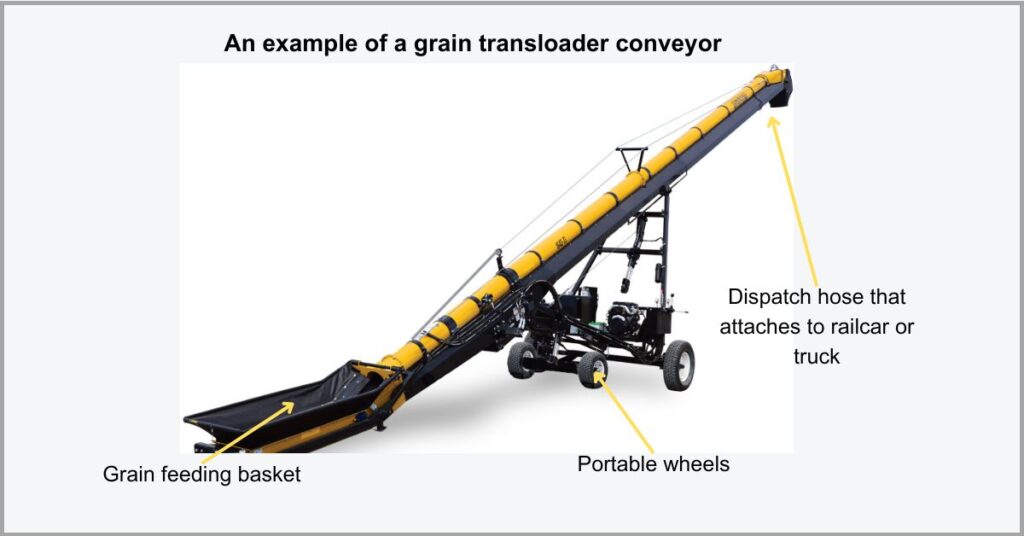
But what is a transloader conveyor and how does it work?
This is essentially a belt-driven system that enables you to transfer large amounts of bulk goods. It’s commonplace during rail to truck transloading because of its ability to complete grain and mineral transfers quickly and safely.
While there are different types of transloader conveyors to consider, some of these transloading tools are partially or completely sealed with a pipeline-like design.
This design limits grain and material spillage at large, thereby reducing the amount of product lost during transloading and the amount of pollutants released into the air. As a result, conveyors are great tools to help you improve eco-friendliness and compliance.
9. Automated guided vehicles
How much do you spend on labor?
When your transload facility dedicates a huge chunk of its revenue on expenses such as labor, you’ll create an unsustainable business model that not only obstructs success but also raises the risk of business failure.
Without automation technologies like automated guided vehicles, labor needs for your transloading yard increase, consequently inflating operational costs.
In 2023, labor costs alone accounted for 31.7% of operational expenses for warehouses and distribution centers, according to a Warehousing & Fulfillment survey. This figure is as high as 65% for many transloading facilities.
So it’s very clear why automation technologies like automated guided vehicles (AGVs) are extremely important in modern transloading.
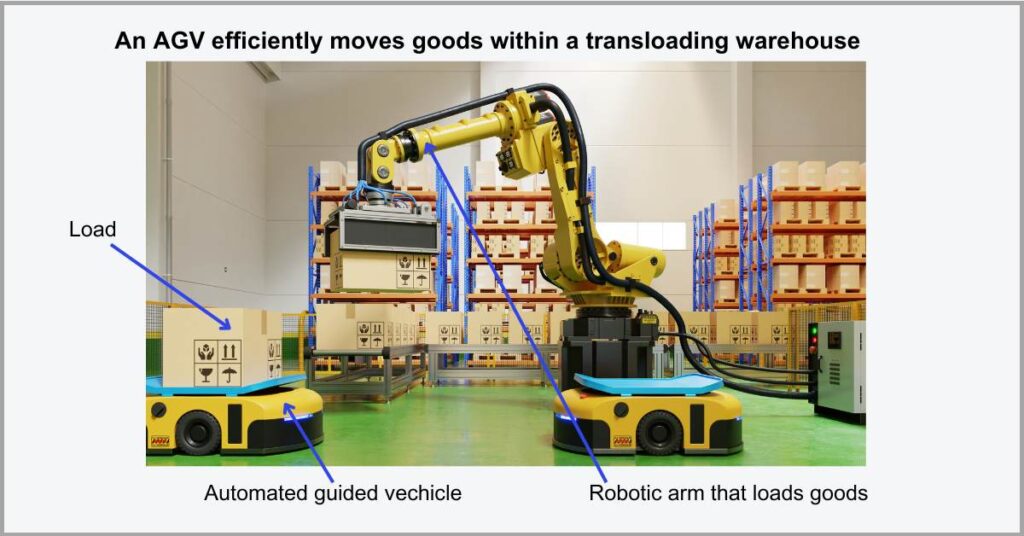
AGVs are key logistics technologies that make the movement of goods within your transloading yard and warehouse more efficient.
They’re among the most popular warehouse automation trends because these vehicles operate autonomously. In other words, there’s no need for a human operator since they can work independently and this lowers your facility’s staffing needs.
They also reduce dependence on human laborers by taking over truck loading and unloading operations, particularly when you’re transloading very heavy loads.
Modern automated guided vehicles even go the extra mile to perform retrieval and put away chores, which enable you to get tasks done quickly with a very lean workforce.
10. Automated picking systems
Picking is an important part of your operations.
Your transload facility may store palletized goods in its warehouse, creating the need for efficient record keeping so that you can retrieve items quickly during pickups by carriers.
However, when your picking processes are largely manual, massive inefficiencies tend to crop up that throw off track loading processes and delay shipments.
It’s alarming to note that 22% of warehouse managers said picking is the most problematic area of the operations, according to a Bluestar survey. This made it the second biggest challenge after inventory management and cycle counting.
More specifically, these businesses admitted that slow picking operations and errors were the biggest contributors to their picking problems.
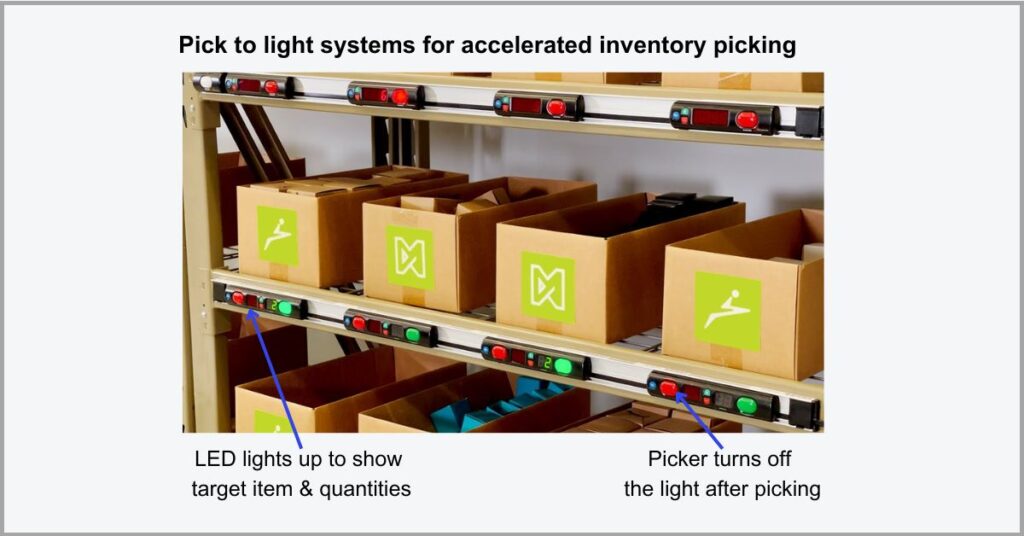
Automated picking systems swoop in to save the day and boost efficiency.
There are different types of these equipment but one of the most common ones is a pick-to-light system. This technology involves the use of lights to identify goods that your pickers need to retrieve for loading onto a waiting truck or railcar.
Typically, it is paired with the best warehouse management systems. This is done to improve inventory visibility and provide the data necessary for mapping the location of items within your transload warehouse or yard.
With automated picking systems, you can optimize movements within large transload facilities, thereby minimizing travel time for transload operators to boost productivity.
Conclusion
Outdated transloading equipment is bad for business.
They are often slow and inefficient and therefore do more harm than good.
In fact, failing to use the right transloading tools can decrease worker satisfaction and productivity, massively lowering your transloading throughput rate.
A survey by Lucasware revealed that 74% of logistics workers are willing to take pay cuts in exchange for better equipment to do their jobs. This is because of the massive productivity impacts the right tools have.
By incorporating the latest transloading equipment solutions we’ve discussed today, you can improve productivity and worker satisfaction. It’s also important to invest in the right transloading software to help you get the most out of your equipment.
Click here to start your free trial of transloads.co and access important efficiency-raising features.
You can augment our software with barcode scanners and other transloading equipment to improve inventory visibility and increase logistics efficiency for your business.