10 Essential Tips for Effective Railcar Switching Operations in 2024
Want to improve railcar switching operations?
The stakes are very high to get railroad logistics strategies like switching right.
When railcar switching processes are slow and inefficient, you can easily experience track congestion that stalls rail shipping operations.
Unfortunately, railcars spend 62% of their time in rail classification yards, according to a SageJournals study. While several factors are responsible, poor railcar switching significantly contributes to these delays.
This is why we’ll discuss important railcar switching tips that can help you ensure railcar switching happens quickly, efficiently and safely to increase throughput. Consequently, you’ll be able to reroute shipments faster to stop cars from piling up.
When this happens, carriers can resume shipping faster, thus ensuring that freight reaches customers on time to improve customer satisfaction and your reputation.
In this article, we’ll discuss essential tips for effective railcar switching operations in 2024 to help you minimize delays and massively increase throughput.
Let’s get started.
1. Streamline switchman communications
How do you communicate with switch personnel?
Railcar switching can be a complex operation where you work with multiple rail yard crew, who need to work together to simultaneously perform various processes. These range from inspections and loading or unloading to rail car repair and switching.
When your rail switching teams aren’t in sync, this can result in switching delays and even serious risk of injury and freight damage for your rail yard.
In fact, in a survey by the Economist Impact, 44% of workers singled out poor communication as the leading cause of workplace delays or failures. They blamed this for loss of morale and said it contributed to huge and irrecoverable revenue losses.
When it comes to rail switching, the stakes are even higher with poor communication inviting chaos that leads to accidents and costly damages.
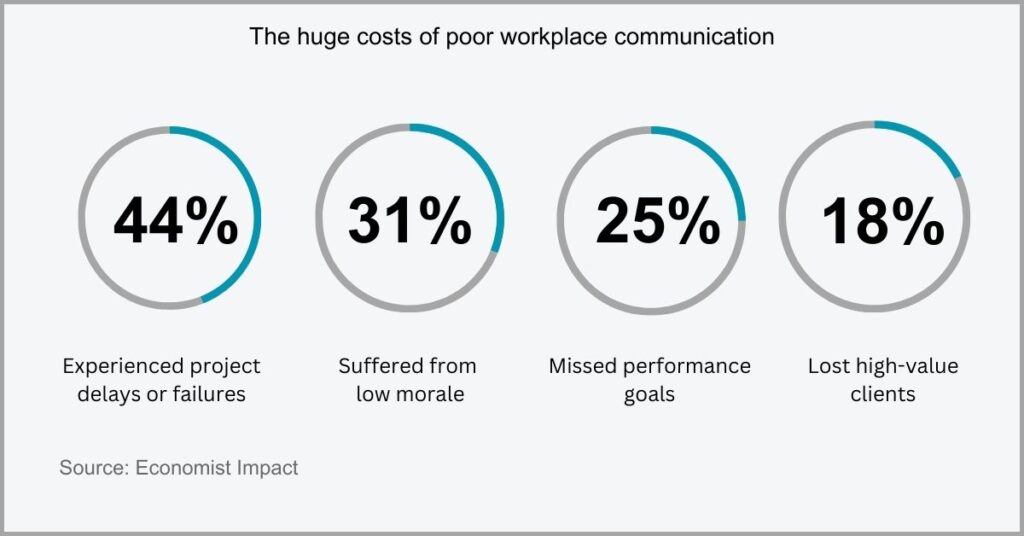
One of the first steps towards better rail switching teamwork is enhancing communication across multi-level switching operations.
When you can communicate more effectively and in real time with switching crews, it becomes easier for your transloading or intermodal shipping rail service to coordinate activities and prepare railcars for different phases of switching operations.
To improve team communication, it’s best to augment existing technologies you may have like two-way radio with modern technologies that tear down communication silos. Some great examples include Click Up and Slack.
These tools enable you to gather team communication in one place, while enabling real-time and documented messaging to improve shared decision making.
You can easily retrace who said what and when,and, more importantly, allow for information to flow freely across different crews to improve collaboration and efficiency.
2. Improve ETA calculations
Getting accurate ETAs often involves a lot of work.
You may need to perform back and forth communication with the railroad company, or even have to rely on manual strategies that don’t factor in real-time variables that can result in unexpected delays. All this makes it difficult to anticipate the arrivals of railcars.
When your ETA estimates are off the mark, this can hurt logistics operation planning and also throw off your shipping delivery schedules as well.
In fact, 35% of rail shippers said that railroad companies are unreliable, according to a survey by the ACD. They rarely get notified of delays or scheduling changes and often have to find out the hard way.
So you need to reinforce your process of obtaining ETAs with alternative solutions that help you predict rail car arrival times more accurately and efficiently.
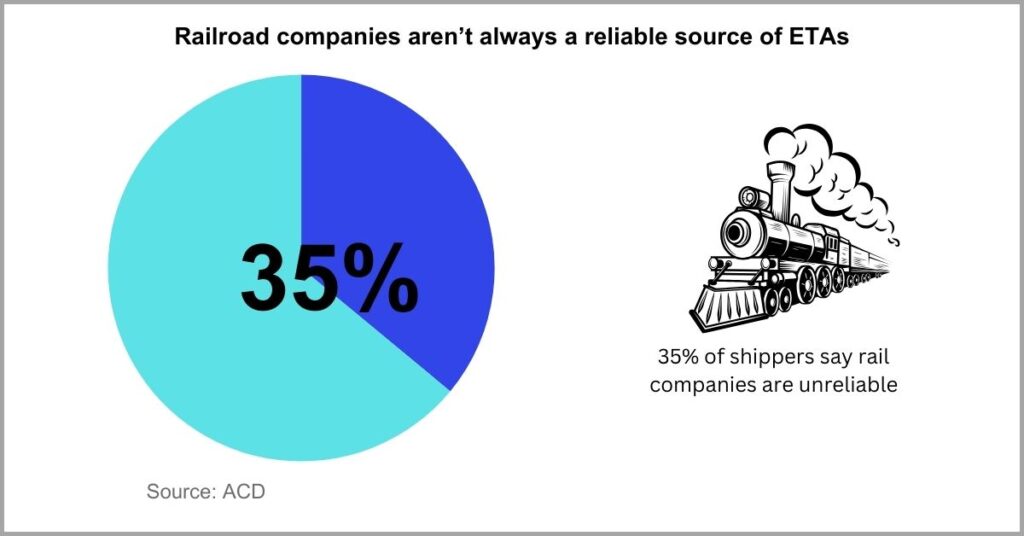
But how can you improve ETA calculations for your rail switching company?
This is where the best transload management software, which can automatically track inbound and outbound railcars comes in handy.
By incorporating various rail tracking technologies, including GPS, you can monitor the location of cars in real time to determine in-transit durations. Some of these tools also notify you in case of unexpected events on the railroad to inform corrective actions.
On the other hand, the ability to track outbound cargo is also key to helping you confirm whether a rail car made it to its target destination.
With accurate ETA estimates, you can plan important operations ahead of time to streamline rail switching operations, including inspections and offloading. In addition, this also reduces manual followup strategies to improve productivity.
3. Use digital receiving checklists
What’s the first thing you do after receiving shipments?
Your preliminary routine tasks may entail checking that the stated inventory matches what’s actually in the railcar in terms of item descriptions and their quantities. Additionally, you’ll also want to check goods for any transportation damages.
If you rely on paper checklists to process rail shipments, this can hurt rail switching efficiency and also lead to inventory mistakes because of human error.
Unfortunately, a single misshipment can cost you up to 21% of its order value, going by a Pitney Bowes survey. So the reverse logistics expenses will only keep stacking up the more inventory items you transfer to the wrong railcars.
This strongly emphasizes the need to digitize inventory checklists, which can help minimize inventory errors to ensure more accurate railcar switching.
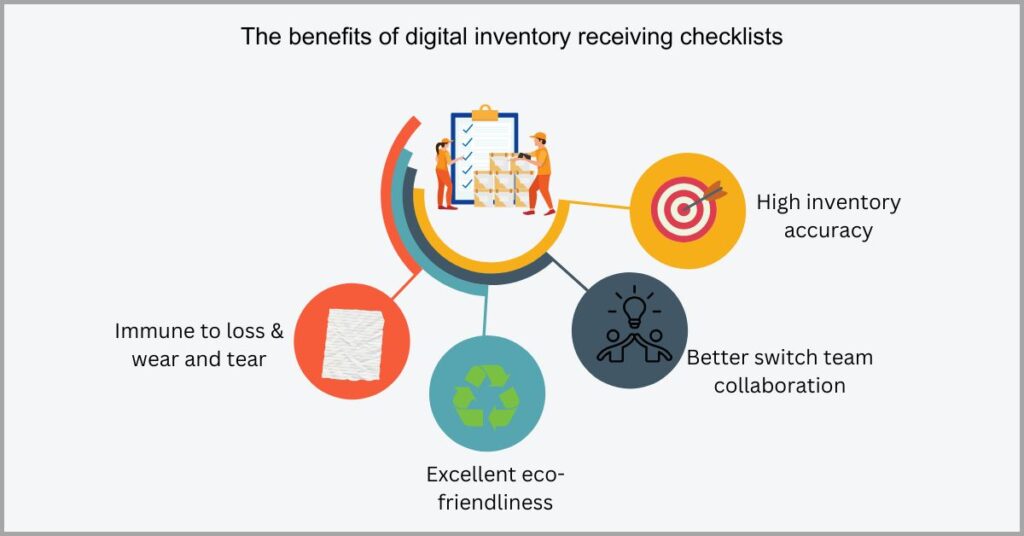
Fortunately, making a digital receiving checklist is very easy.
You can use various online graphic tools to get checklist templates and then make minor adjustments to match the unique needs of your railway switching operations.
Such solutions, however, aren’t the most ideal for the job due to feature limitations.
Instead, I recommend proven yard management software solutions such as transloads.co. In addition to giving you digital tally sheet templates, you’ll also be able to get bar code scanning features for quick, fast and highly accurate inventory counting.
When this happens, you can accelerate inventory processing, and get to important tasks like breaking up trains into individual railcars for shipment much faster.
With digital receiving checklists, which are easily shareable, you’ll also streamline the coordination of switching processes to increase productivity and efficiency.
4. Assign switchman tasks strategically
Efficient task planning is key to success.
When it’s unclear about who needs to do what and when, which can be a huge problem in complex switching operations, this can create accountability issues and make it difficult to identify operational bottlenecks and evaluate switchman performances.
Ultimately, the lack of efficient task planning, prioritization and allocation kills productivity, hampering your ability to meet deadlines & customer expectations.
A McKinsey study revealed that 83% of businesses identify proper resource allocation, including human workers, as a key lever for better performance, growth and efficiency. Important as it is, many of these businesses still confessed to struggling to achieve it.
One critical reason for this is a poor understanding of where resources will yield maximum value thus necessitating the need for strategic task planning & allocation.
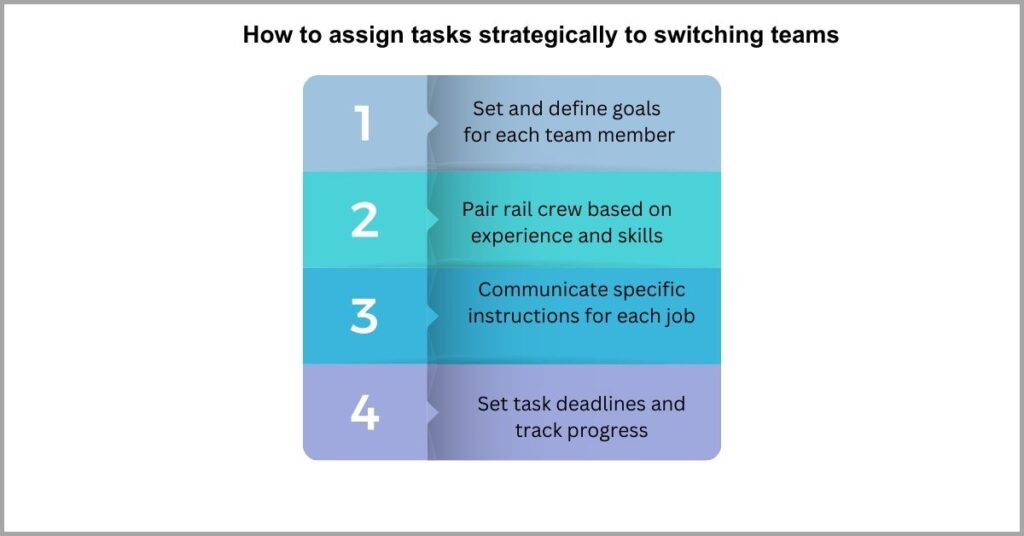
But how exactly can you achieve strategic task allocation?
You may need to turn to task management software to help you out. This can enable you to assign various operations to different members of your team depending on their unique skill sets, location and availability, among other criteria.
If you’ll be working with transload service companies and other supply chain partners, such a system plays an even more critical role in enhancing efficiency.
It lets you create custom workflow paths that define standardized procedures regarding how loading, inspection, cleaning and railcar storage, among tasks, are to proceed. This helps to ensure everything happens sequentially to minimize delays and reworks.
Complete with task completion and other key KPI notifications, these tools can also help you improve switch operator productivity to increase throughput in rail switching yards.
5. Perform preventive rail maintenance
How often do you perform preventive rail maintenance?
When neglected, rail switch defects can go unaddressed until the very last moment when it may be too little too late. These defects can easily result in switching railcars to the wrong tracks, leading to switchmen, brakemen and freight conductors being struck.
On top of that, unaddressed rail switch problems can also impede train operations, resulting in disruptions that cost you time, labor and revenue.
A study by MDPI revealed that 40% of total railway failures result from switches and crossing equipment defects. This proves that rail switches are the most vulnerable aspect of your operations and that you need to keep a close eye on them.
When you implement routine, preventive rail maintenance strategies, you can spot and correct rail switch defects before they cause harm and revenue loss.
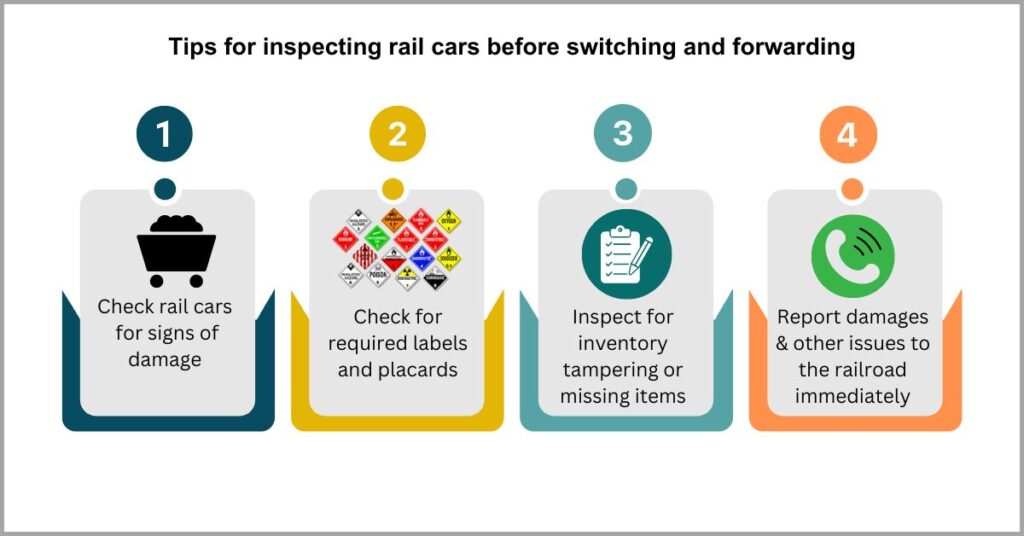
In order to be proactive with railway switching, rail line and even rail car maintenance, you need to routinely collect data about their status and standardize railcar inspections to determine corrective actions before failure or breakdowns.
This data should be about important KPIs that reflect the performance of switches, cars and rail lines at large to enable you to spot any deviations in normal performances.
Notably, you may need to leverage warehouse and logistics innovations, including rail diagnostic tools like fault loggers and data recorders. These can highlight common and recurring problems on switches and rail equipment to help find a permanent fix.
When you’re more proactive than reactive about rail maintenance, you can ensure higher availability of tracks, railcars and railway switching equipment to reduce operational delays, improve rail safety and increase productivity and revenue.
6. Track empty railcars
Managing empty railcars is a routine rail shipping task.
However, in a complex rail yard with so many different tracks, it’s so easy to lose track of rail car’s you’ve unloaded and now presently sit empty. This may necessitate constantly walking back and forth to reconcile empty cars.
When empty trail car tracking is poor, fleet utilization also decreases while this increases rail switching operational costs due to rail demurrage penalties.
In 2021, an STB study revealed railroads got 1.18 billion in demurrage fees in the first three quarters of the year. This is the highest demurrage revenue collected since 2011, showing an alarming trend of increasing railcar detention.
One key reason for this concerning situation is poor railcar visibility, which makes it difficult to locate empty railcars and track the duration you’ve held them for.
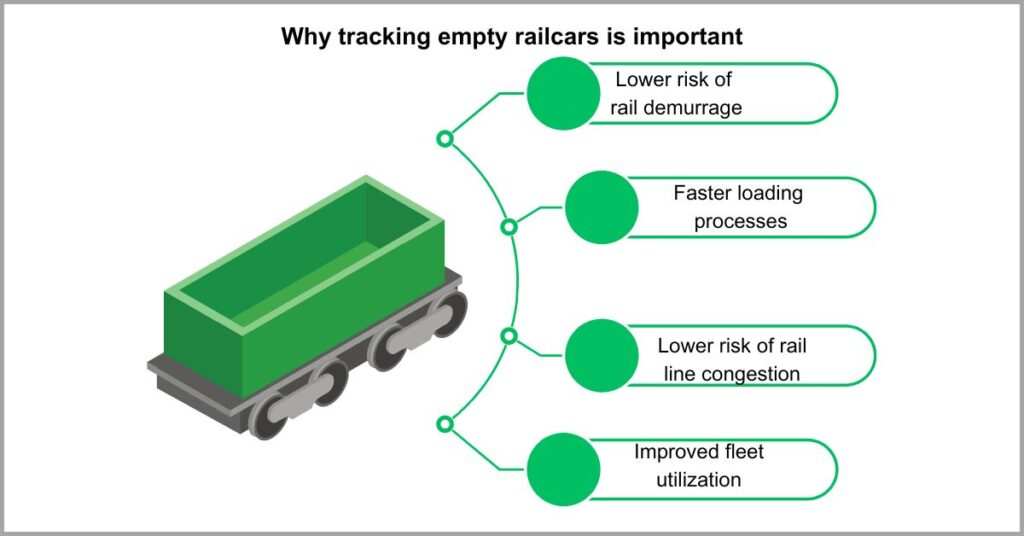
But how can you improve empty railcar visibility?
Well, it helps having a dedicated rail line or two, specially set aside for empty rail car placement so that you know where your empty railcars are at all times.
This isn’t always possible however because all your rail lines may be actively in use, necessitating constant car position switching.
In this case, yard management software are the better option for tracking empty cars.
These can provide key timestamps of when a car was placed on the rail, including the content of its inventory. With this information available on a centralized dashboard, you can view the locations of all your empty cars instantly and more effortlessly.
Consequently, this makes it easy to plan switching operations through strategic empty railcars to track assignment while it also improves fleet capacity utilization.
7. Improve rail movement safety
Are you confident in the safety of your switching operations?
Rail switching can be a very dangerous process. You have human switch operators working in very close proximity to railcars that can easily weigh up to 280,000 pounds. One wrong move and you could be looking at a serious injury in the rail yard.
That said, rail switching accidents are highly undesirable because they lead to productivity and financial losses in addition to decreasing staff morale.
An NSC study discovered that there were 3,316 rail employee accidents in 2022. While this represents a significant decline from the past years, they still remain a key threat to your rail switching operations.
Some of the reasons why many rail switching accidents happen revolve around negligence and a lack of safety awareness among rail employees.
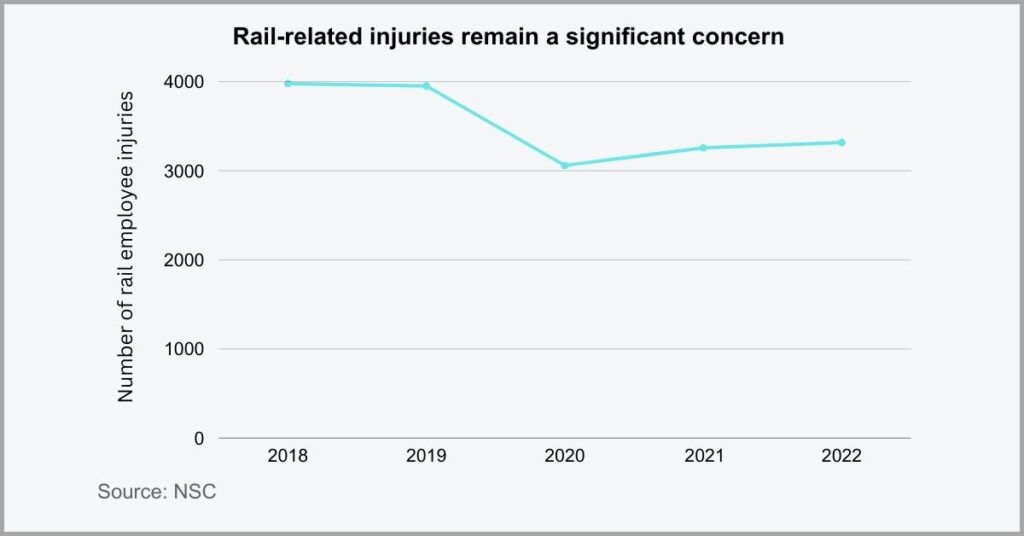
So it’s important to create an operational rail safety awareness program.
It can help you establish accident-free railcar switching operations that reduce disruptions and bolster your railroad logistics strategies to improve rail yard safety and keep your team functioning like a well oiled machine.
That said, to improve rail movement safety, you need to have a plan to guide each rail switching operation or project, down to every movement involved.
This may entail having dedicated grounds personnel proceed to inspect rail tracks before you receive inbound cargo. They can remove blue flags, unused chocks, and other derailers and trip hazards as they preset switches.
It’s also prudent to set up an elevated guard post to oversee switching operations.
This can help prevent vehicles and pedestrians from accessing intersections and crossings to ensure safe and efficient rail switching and movements.
8. Reduce yard travel time
Your switchmen spend a lot of time traveling.
They move back and forth across the rail yard to couple and uncouple trains, operate the brakes, load and unload cargo, and perform many other duties and they may do so primarily on foot.
That said, when movements are inefficient and slow, you can lose a lot of direct labor time, which only compounds the gravity of existing labor shortages.
It’s alarming to note that workers waste nearly 4 hours of each work day on various iterative tasks, according to findings from a Zippia survey. For rail operators, one of the biggest distractions are inefficient yard movements that increase travel time.
Considering an average switchman salary of $21 an hour in the US, this can mean $84 in daily losses if this professional loses the same amount of time.
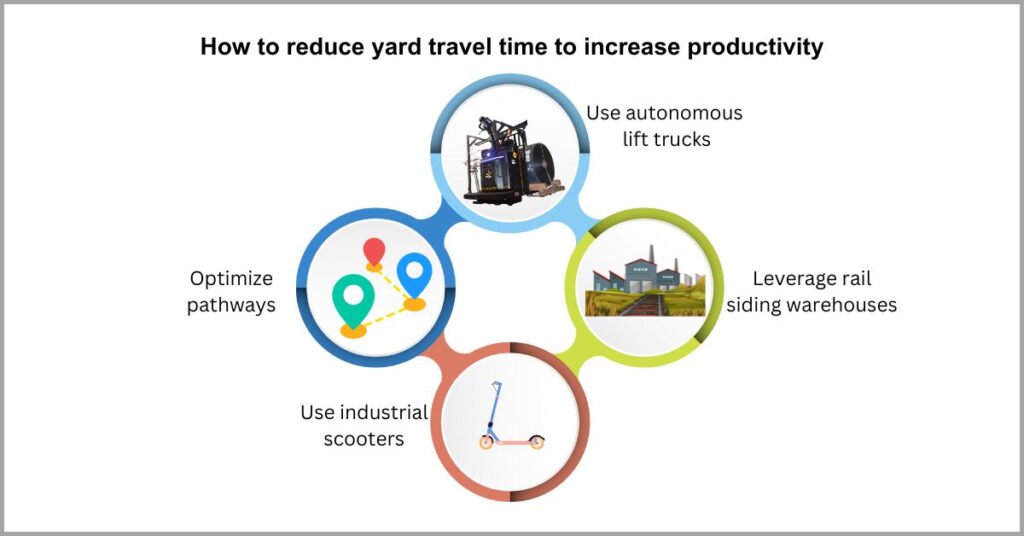
But how can you reduce travel time for switching crew?
One of the most important rail switching strategies to ensure each movement is purposeful and efficient is path optimization. A great transload yard management tool can help you out with this to reduce travel time.
That said, some key features of transloading software to consider here are virtual maps.
These tools use various path optimization algorithms, taking into account user start and end points, among other factors, to suggest efficient paths to follow. This helps ensure that every movement is efficient in relation to subsequent tasks.
On top of that, it may also be prudent to consider industrial scooters and bicycles.
In a very large and complex rail yard layout, these tools can help ensure fast and safe movement across the railyard and in between workplaces to increase productivity.
9. Avoid overloading railcars
Want to make your switching operations more profitable?
It’s tempting to overload railcars, especially when there’s a shortage of cars and you don’t have a lot of personnel to spare. Alternatively, you may also be tempted to exceed a car’s acceptable limits in a bid to maximize utilization and profits for your business.
However, rail car overloading can have the opposite effect on revenue because they increase the risk of derailment, which only disrupts your operations.
A Wailey study recently revealed a 24% increased risk of derailment for freight trains with 200 cars, which dropped to 11% for trains hauling 100 railcars. This is proof of the increased risk overloading poses.
Besides creating unsafe conditions for your switchman operations, this can also attract huge overloading penalties and re-weighing expenses by the railroad company.
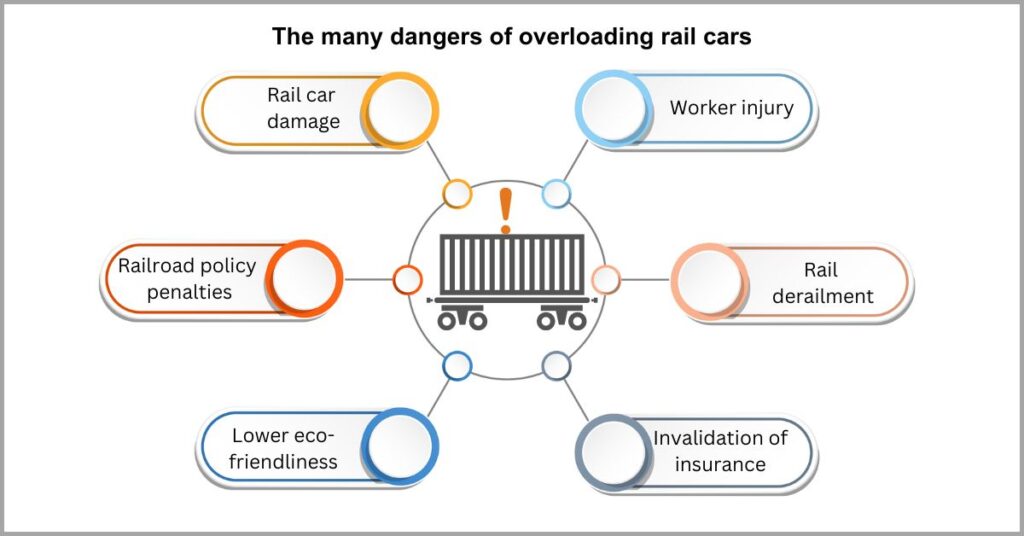
Railcar overloading can happen purposely or accidentally.
To ensure negligence isn’t to blame, it’s important to see to it that your rail switching crew follow proper railcar loading and unloading procedures to prevent overloading.
This necessitates rigorous staff training that reinforces standardized processes, where your staff check for railcar’s published weight limit before each job. If this information isn’t readily available, you should liaise with the railroad company to get more details.
Additionally, I also recommend leveraging technology to keep track of rail car weights.
One of the top benefits of transloading software is that it helps you keep track of laden, tare, gross and net weight. With this information, you can prevent overloading.
When you load railcars optimally, this also reduces wear and tear to lower maintenance expenses while also minimizing disruptions to keep your operations flowing.
10. Optimize railroad warehousing
Do you rely on a warehouse to hold goods?
You may have a railroad siding warehouse for your rail switching yard to store offloaded goods from railcars as they await loading onto an oncoming train. This warehouse is especially important for ensuring the efficient movement and safe holding of cargo.
However, when warehousing operations are inefficient, this can mean slow loading and unloading processes that ultimately delay rail shipping.
A study by Intermec revealed that 42% of warehouse workers lose up to 30 minutes daily to various process inefficiencies in their warehouses. Factor in the number of employees in your switching crew and the productivity losses become so big.
Besides hindering productivity, an inefficient warehouse can also lead to railcar congestion that attracts demurrage, reduces your throughput and decreases revenue.
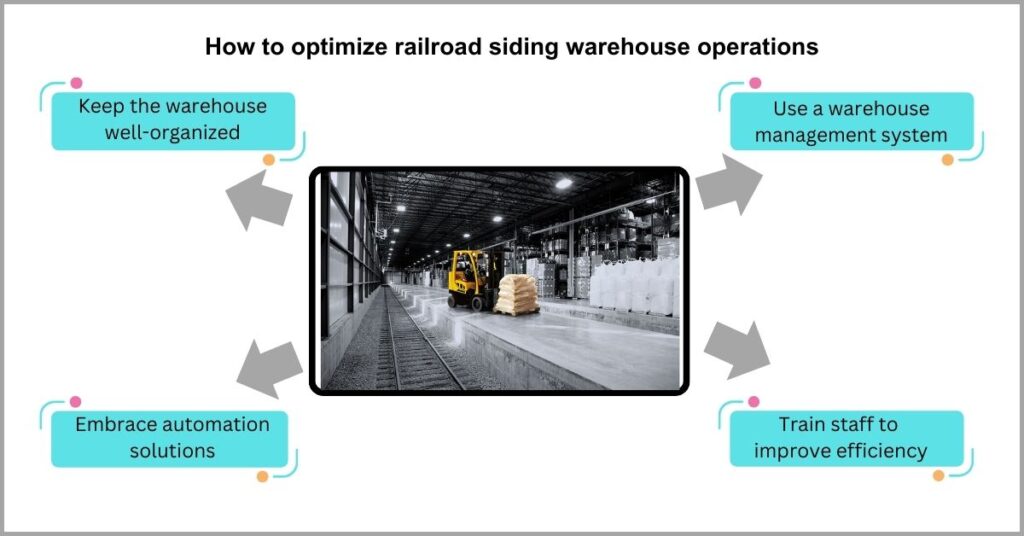
If you lack railroad-siding warehouses, in the first place, you should consider investing in one because they can massively improve rail switching efficiency.
For example, they enable you to direct cars into warehouses holding freight, where your switch crew can directly unload shipments from the warehouse into the car without traveling. Loading operations can also similarly take place efficiently.
If you’re worried about generating enough ROI to substantiate the investment, I suggest that you also invest in other profitable warehouse business ideas in times of low demand to generate additional revenue to keep the lights on.
That said, you may need to turn to a warehouse management solution to optimize warehousing tasks and increase productivity.
These can help you automate inventory tracking, and, more importantly, reveal important performance data for improving railcar throughput in your warehouse.
Conclusion
Railcar switching can be a complex puzzle.
You’re trying to achieve fewer moves, reduce walking distances and achieve optimal railcar coupling sequences.
With poor railcar switching, you’ll notice increased expenses because of higher fuel consumption and the inefficient use of switch crew and equipment.
A Costmine Intelligence study revealed a $62 cost increase in rail freight transportation expenses between 2018 and 2023. Of course, several market factors are to blame but inefficient railcar switching plays a significant role.
By prioritizing the critical railcar switching pointers we’ve discussed today, however, you’ll achieve faster cycle times and make your switching operations more profitable by reducing switching expenses and increasing efficiency.
More specifically, remember to streamline switch crew communication, enhance ETA calculations and use digital receiving checklists to boost productivity.
In addition to increasing cost-efficiency, these tried-and-tested strategies will also ensure more effective railcar switching to also improve rail car fleet utilization.