10 Ways Robotics is Transforming Warehouse Management Operations in 2025
Ready to revolutionize your warehouse?
Many of the best transload service companies are turning to smart robotics.
These technologies can help you lower your labor needs and expenses, which may significantly limit your small transloading business’s profitability.
Labor expenses claim 31% of warehouse revenue on average, according to a study by Warehousing and Fulfillment. In some cases, it’s hogging twice as much, and massively limiting profits for these businesses.
By leveraging the power of robotics in warehouse management, you can automate a lot of labor-intensive tasks for your small business. These include processes such as packing, palletizing and even cleaning, to help lower your labor requirements.
These technologies are therefore ideal not just for lowering operational expenses but even filling labor shortages and increasing productivity for your warehouse business.
If you’re interested in streamlining warehouse yard operations, check out this article I wrote about yard management tips for better cost-efficiency.
In this article, we’ll discuss some crucial ways robotics is transforming warehouse management operations in 2025 and how they can help you improve profitability.
Let’s get started.
1. Automating loading and unloading
Want to improve your warehouse’s throughput?
Well, I recommend that you consider using robotics in warehouse management, and in particular, truck loading and unloading automated systems to help you out.
Truck loading and unloading may be a common everyday task for your warehouse, and if it’s inefficient, you could lose a great amount of productivity.
It’s interesting to note that 40% of warehouses are interested in investing in truck loading/unloading robots, according to a study by PRG. This signifies the highest intended use case when it comes to robotic automation systems.
Other popular technologies that warehouses are seriously considering include transport robots, sortation machines, collaborative aisle pickers and cleaning robots.
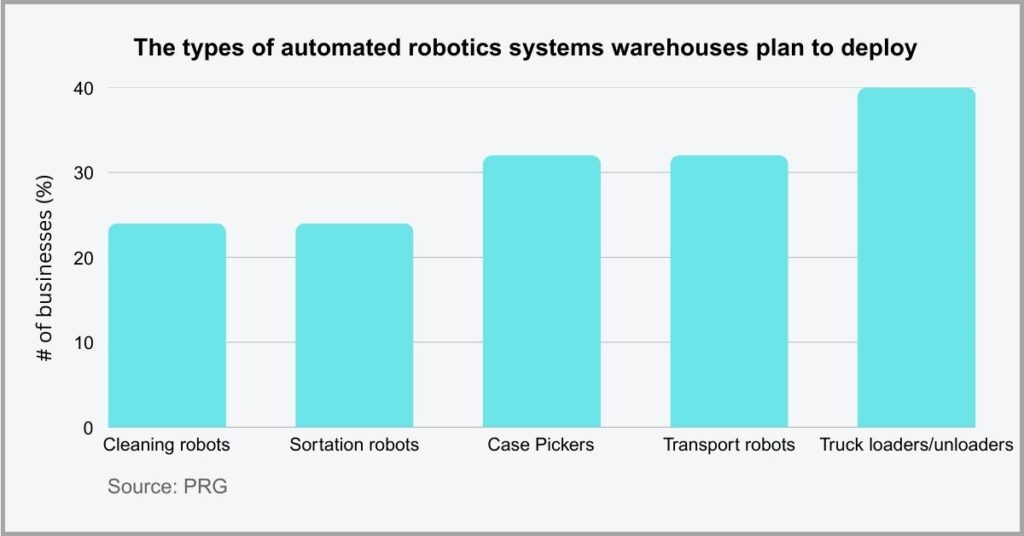
With automated loading and unloading robots, you can automate the movement of goods from truck to warehouse and vice versa. This results in increased efficiency and throughput since they don’t experience fatigue, which can create performance dips.
In order to get the best out of these robots, I recommend using a transload management software. It gives you access to real-time data, which can help you improve your planning processes.
For instance, try our transloads.co software for free, and you’ll get advanced incoming and outgoing shipment tracking for your warehouse business.
This information, coupled with real-time inventory tracking capabilities and other advanced data analytics, enable you to improve robot resource allocation.
2. Enhancing palletization operations
Palletization is an important practice.
If you run a transloading warehouse, it becomes even more crucial because it helps you to consolidate freight into one package. This enables your workers to quickly and efficiently transport goods across your warehouse.
Additionally, palletization also helps you to better use vertical space, enabling you to avoid poor floor space utilization that lowers operational capacity.
A survey by Statista revealed that 36% of warehouses and distribution centers cited inefficient space for inventory as a major issue. When space is scarce, the amount of inventory your business can hold is greatly limited and so too are your profit margins.
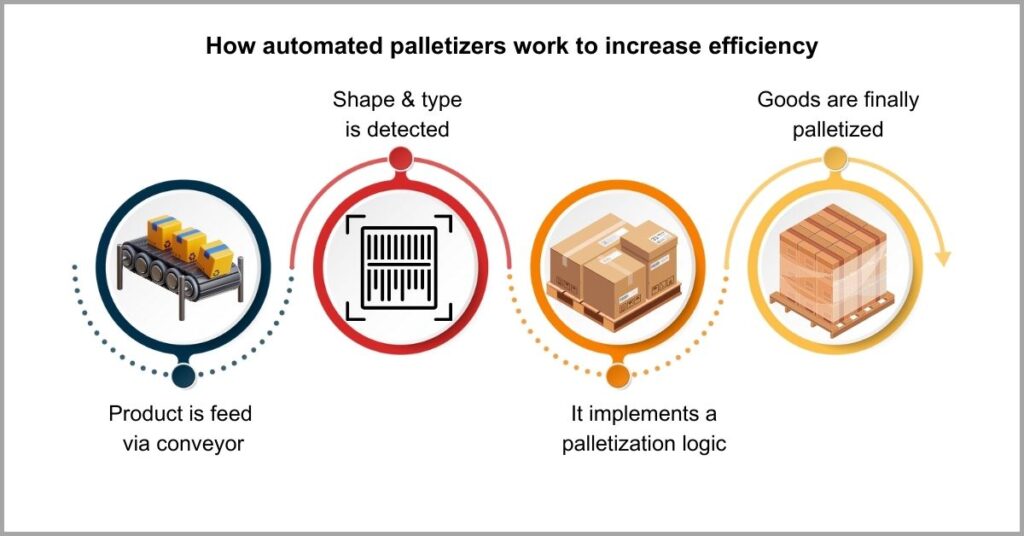
It is for this reason that I recommend using robotic palletization systems, which represent one of the most exciting use cases of robotics in warehouse management this year. Besides space efficiency, they can also improve throughput during palletization.
But how do robotic palletizers work exactly?
First, they perform identification using sensors & then grip and retrieve target products. You may use them in combination with top transloading equipment, like forklifts to move heavy-duty items although some of these robots are completely self-sufficient.
Overall, these robotics can make adjustments in real time based on a stacking pattern or real-time inputs like the size or type of commodity to help increase space efficiency.
3. Assisting with order fulfillment
Struggle to keep up with customer demand?
The modern day customer has gotten more impatient over the years, and they expect you to fulfill and deliver their orders within the shortest possible time frame, which is usually the same day.
If you don’t have the right technologies in place, then you may fail to meet customer expectations and this can lead to lost business for your warehouse.
In 2024, at least 14% of warehouses said that keeping up with customer demands for rapid delivery is a huge struggle, going by a recent AutoStore study. This made it the joint fourth top challenge that’s keeping warehouse businesses from growing revenue.
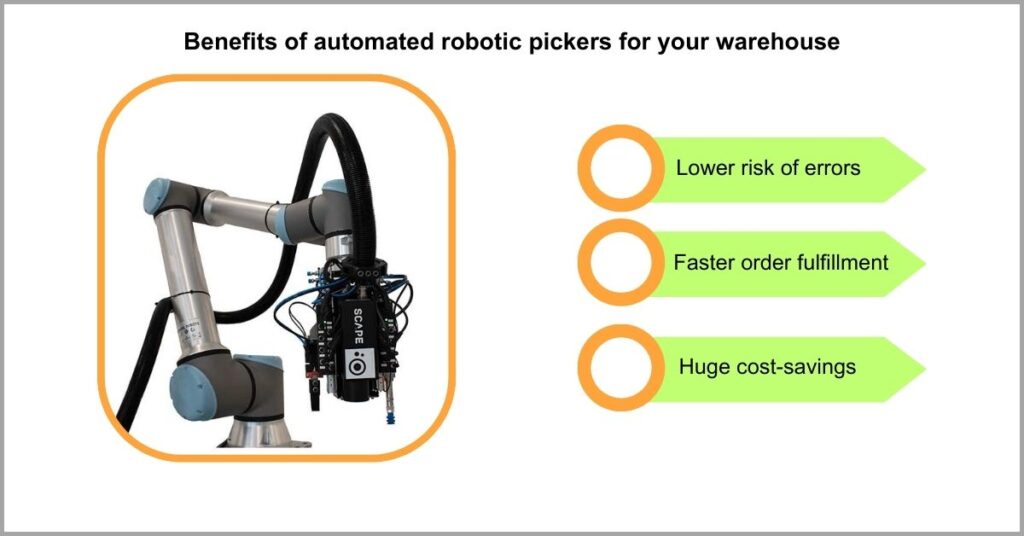
If you tap into the latest logistics innovations revolutionizing the industry, and particularly the use of robotics in warehouse management, you can fast track order fulfillment to easily meet your customer’s desired shipping timelines.
Some robots that can come in handy for this include automated picking systems.
These machines are equipped with advanced computer vision technologies, which enable them to recognize inventory items. They also typically have a robotic arm for picking a variety of products including bins, boxes or individual items.
Additionally, it may also involve the use of robotic packing systems, which can sort and place items in optimal configurations to reduce damage and improve space utilization.
4. Improving heavy-duty inventory movement
Forkflits are a popular warehouse equipment.
They enable you to quickly and efficiently move very heavy cargo around your warehouse, offering greater capacity and strength compared to pallet jacks. The problem though is that traditional forklifts are typically dependent on human drivers.
With the grippling labor shortages in warehousing, you may not have sufficient personnel to operate forklifts and perform other important tasks.
A study by Instawork revealed that at least 73% of warehouses are struggling to find enough labor to meet their business’s demand. One particularly huge problem is recruiting skilled and competent forklift operators.
These are kinds of challenges that you can solve by using robotics in warehouse management.
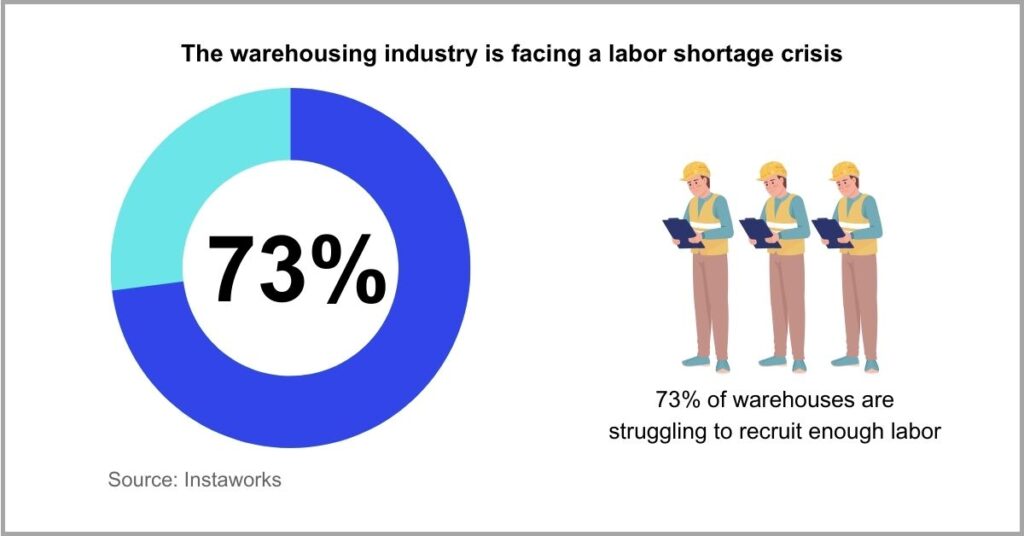
For example, you can leverage autonomous forklifts, which can operate without a driver to help plug any labor deficiencies you may have when it comes to this department.
But it’s not just about sealing worker shortages alone.
It can also help you improve rail transloading safety by averting potential accidents. With advanced object detection and collection-avoidance technologies, these equipment can adjust routes dynamically to avoid collisions and other incidents.
Aside from proximity sensors for detecting nearby humans, these special types of forklifts also have emergency stop mechanisms & failovers. These immediately halt any movements in case unexpected objectables appear in the route to further avert danger.
5. Automating cycle counting
So what is cycle counting & why does it matter?
Cycle counting is simply the process of checking your inventory records against the physical inventory that you actually have on hand. It’s done periodically and often involves a predefined portion of your inventory.
That said, when cycle counting is largely manually, it becomes very time consuming while you may experience stock discrepancies and misinformation.
A survey by BlueStar revealed that 50% of warehouses struggle with inventory cycle counting. This is due to the heavy time commitment necessary for performing regular counts, therefore proving the need for robotics in warehouse management.
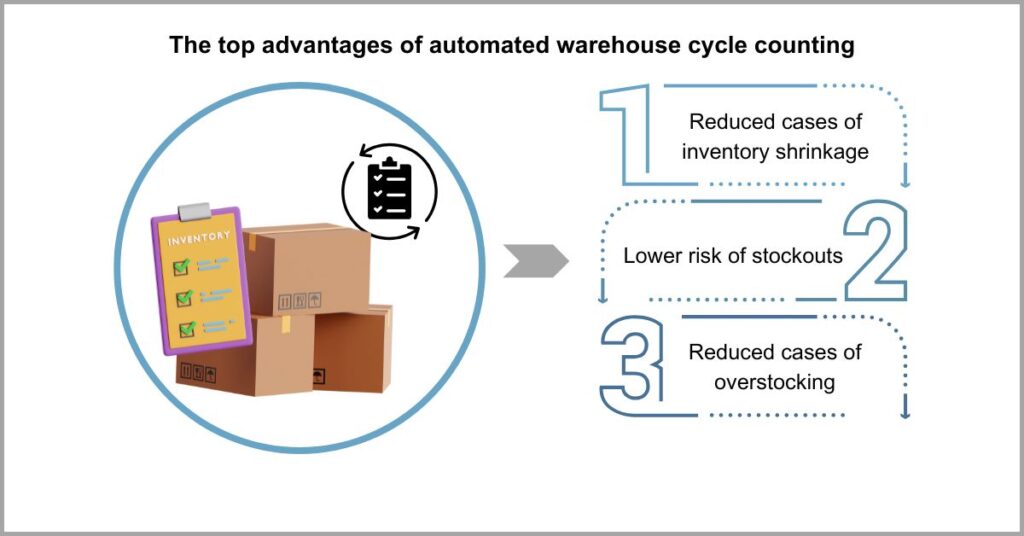
In particular, I recommend using automated cycle counting robots, which can travel across your warehouse and perform period cycle counting scans autonomously.
That said, you also need a great warehouse management system to complement your robot to enable real-time inventory cycle updates and remote access to this data.
So why not try transloads.co for free today? Our software has powerful inventory management capabilities which can help you improve cycle counting processes for your small warehouse business.
With our software and the aid of the right robotics, you can improve efficiency in cycle counting and general warehouse management. Aside from that, you can also quickly identify and sort out stock discrepancies to avoid serious operational disruptions.
6. Streamlining quality checks
Product quality checks are a vital operation.
However, the process can be so time consuming and effort intensive, especially if your small business relies on human personnel to carry out these processes.
When product quality inspections aren’t carried out properly, your customers may receive subpar goods, leading to returns, complaints and negative reviews.
It’s alarming to note that 39% of customers return items they’ve purchased at least once a month, according to a study by Narvar. One of the top reasons for this is customers receiving sub-standard or damaged items.
When returns happen too often, your warehouse experiences reputational damages as well as financial losses associated with the reverse logistics processes.
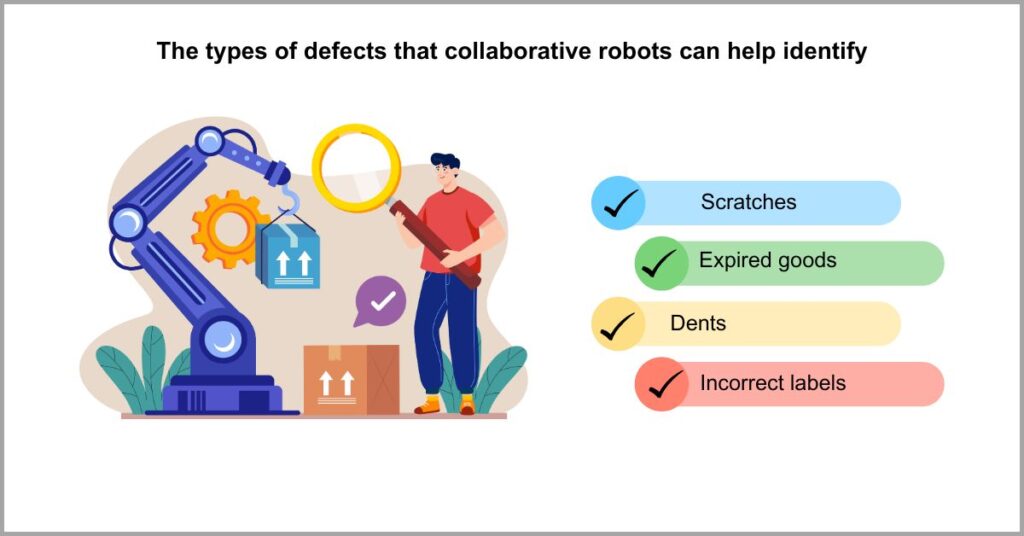
In order to get around this challenge, you should consider collaborative robots (Cobots). These can work hand in hand with your warehouse staff during order fulfillment, helping particularly when it comes to product inspections.
So if you’re looking to start a warehouse business that’s cost-efficient and less susceptible to human error, consider using these types of robotics in warehouse management.
As opposed to their human counterparts, Cobots leverage AI-powered vision systems to detect various defects.
They can recognize issues like incorrect labeling, dents and scratches more accurately, ensuring shippers get very high-quality and damage-free products. In addition, they can also lower your labor needs, thereby making your small business more profitable.
7. Automating warehouse cleaning
So why is maintaining a clean warehouse important?
During warehouse operations as your workers move or even transload different types of commodities between various points, spills and leakages are bound to occur.
If your warehouse is dirty, your business faces the increased risk of slips, trips and falls, creating workplace hazards that may result in OSHA violations.
A study by the US GAO showed there were over 2,500 workplace violations for warehouses between 2018 and 2023. Some of these violations arose from unsafe working conditions contributed to significantly by unclean environments.
With automated warehouse cleaning robots, you can maintain a clean warehouse to eliminate workplace dangers and improve OSHA compliance.
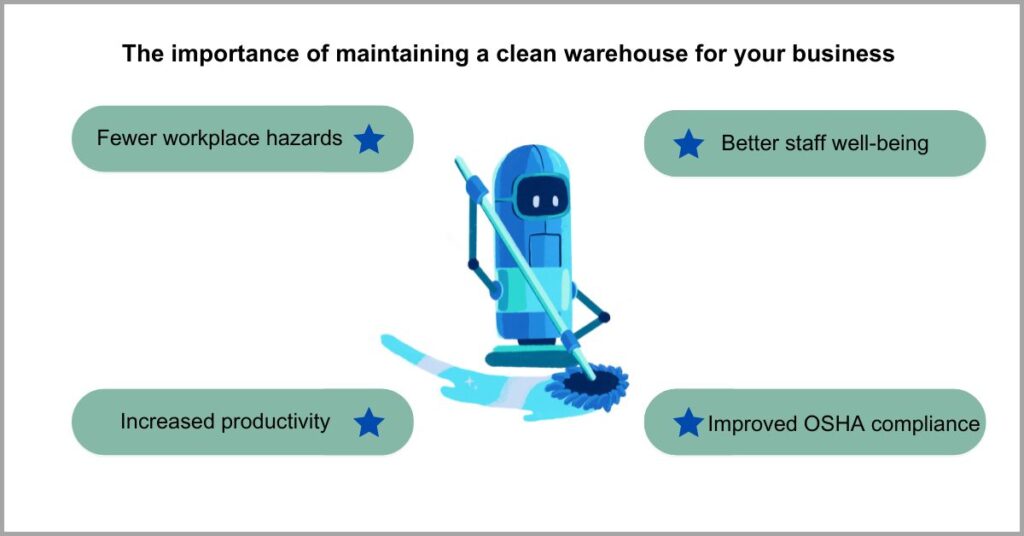
These machines are designed to navigate warehouse spaces efficiently, and identify and even clean up debris that may be left over during transloading operations.
Many automated cleaning robots typically have scrubbers & rollers to ensure the deep cleaning for warehouse floors, and areas that may be hard to reach for human workers such as corners and small pathways, for example.
If you get specialized robotics for handling dangerous chemicals, your warehouse can also improve transloading spill containment, while ensuring very minimal human involvement, thereby increasing worker safety and reducing labor needs as well.
In such cases, they may come with dedicated disinfectant sprayers to neutralize chemicals and even electrostatic sprays to kill bacteria and pathogens in the air.
8. Enhancing material handling
Proper material handling in warehousing is crucial.
It directly impacts your warehouse’s profitability, because inefficient systems can create a lot of unnecessary movements or handling steps, resulting in massive time losses.
What’s more, poor material handling, especially where heavy or bulky items are concerned, can also increase the risk of workplace injuries for your warehouse.
A SCMR study discovered that more than 31% of warehouses implemented conveyor robotics to improve their material handling processes. This made it one of the top three most popular material handling systems.
By incorporating this type of robotics in warehouse management, you can enhance worker safety and also optimize your workflow.
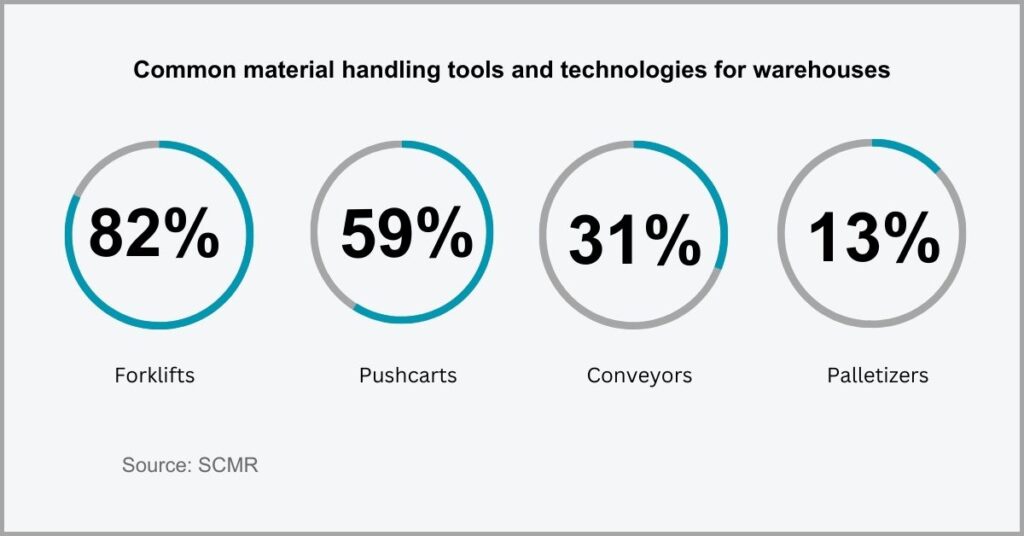
With conveyor robotics, you can quickly move products between different stages during warehouse processing, right from receival to storage or from storage to picking.
So it can help improve your operations holistically.
If your warehouse performs coal transload shipping, these types of systems can also help you minimize waste. They reduce the risk of material spillage and poor handling by human personnel, allowing you to consolidate or deconsolidate it faster and safer.
When paired with AI and intelligent sensors, conveyor robots can even perform efficiency sorting at very high speeds. So it can reduce cases of incorrect sorting, thereby helping to ensure more accurate inventory management and order fulfillment.
9. Improving shelving processes
So what is smart shelving in warehousing?
Smart shelving refers to a system of robotics, which uses a combination of advanced tracking tools, sensors and even various IoT devices in order to detect when items are added or removed from a shelf.
With the live inventory data they provide, coupled with automatically triggered restocking actions, this technology helps you reduce the risk of stockouts.
In fact, over 70% of warehouse managers believed smart shelving technologies were the most important technologies to watch in 2024, according to a Hopstack survey. I’m certain it will catch on even more this year due to its ability to minimize lost sales.
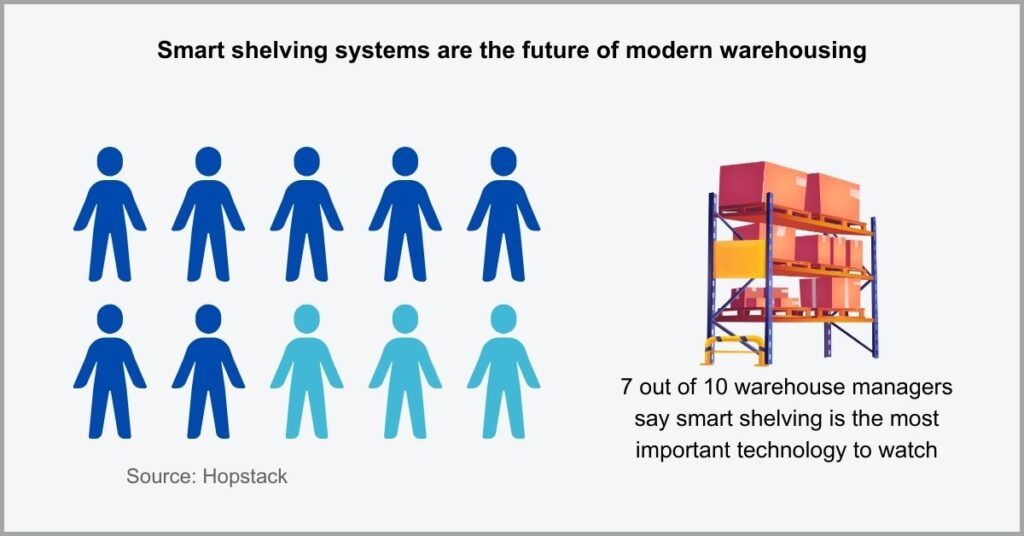
Using sensors or RFID tags, smart shelving systems, which may also adjust shelf configurations, can greatly optimize inventory storage in real time.
But smart shelving isn’t a stand-alone technology.
I recommend pairing it with autonomous mobile robots, which offer the physical power for moving items, as well as excellent warehouse management systems. These can support smart shelving systems with their real-time inventory tracking capabilities.
So improve inventory management and start your free transloads.co trial today to take the power of robotics in warehouse management to the next level.
Our software augments smart shelves, among other robotic systems you may have in place, enabling you to create a smarter warehouse with better inventory accuracy.
10. Creating favorable micro-climates
Cold chain inventory attracts unique needs.
You may need to store these types of perishable items within certain controlled temperature ranges in order to keep them fresh and potent. The problem, however, with manual temperature regulation is that it’s so time and effort-intensive.
With climate-control robotics, you can automate temperature control to avoid human-driven regulation that increases the risk of item degradation & spoilage.
Unfortunately, a survey by Statista discovered that 62% of businesses struggle with proper cold chain handling and temperature monitoring. It’s a problem you can solve by using the right robotics in warehouse management to streamline these processes.
These enable you to create micro-climates within your warehouse to safely store delicate commodities.
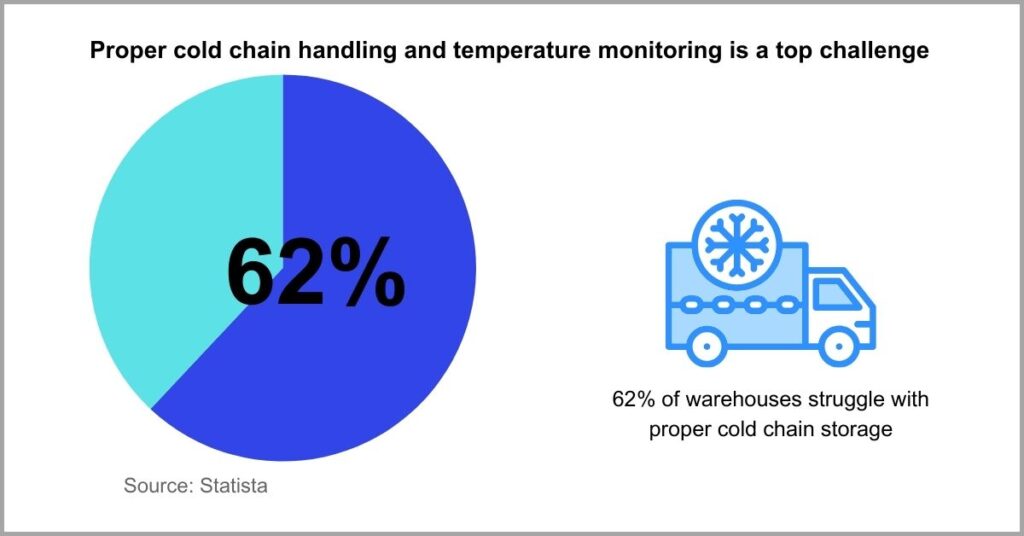
But how exactly do climate-control robots work?
Well, it’s essentially a system of interconnected technologies, and it may rope in robotics, the best transload warehouse management software (WMS) and even IoT technologies.
At the very forefront, you’ll find robots equipped with temperature sensors to continuously track temperature levels in your warehouse. They may also have humidity sensors to also track and adjust humidity levels in different zones.
A great WMS system may serve as the brains of the operations, curating data back into a central dashboard for efficient analysis.
By integrating with your HVAC systems or fans and ventilation platforms, they can automatically adjust airflow to ensure optimal climate regulation throughout.
Conclusion
Growing a warehouse isn’t easy.
Labor constraints are one of the biggest factors that may stand in your way.
If your warehouse doesn’t have the right robotics automation technologies, you may struggle to scale your operations and grow your small business.
Unfortunately, 40% of warehouses are shackled by a lack of robotics automation, according to a recent study by Endava. These companies are consequently struggling with low throughput and growth because of this.
If you take advantage of robotics in warehouse management, you can automate various labor-intensive tasks. Speaking of which, our software can also help set your business on the path of growth.
So click here to start your free transloads.co trial to automate inventory management and increase efficiency and accuracy.
With our software at the heart of your robotics technology ecosystem, you can also centralize data in one place for better operational intelligence for your warehouse.