A Guide to Transloading Containers + 5 Techniques to Boost Port Productivity in 2024
Interested in accelerating port operations?
The effectiveness of transloading and transshipment tasks affect throughput.
When your container transloading processes are slow and inefficient, there’ll be delays in cargo operations, consequently increasing berth idle times for ships.
A WorldBank study revealed that ships spend 59.4% of in-port time performing cargo operations. From this data, it’s evident there’s a lot of time wastage at ports.
In order to help you avoid keeping ocean vessels waiting & compromising your relationship with logistics partners, we’ll examine key methods for transloading containers to raise the productivity of dock workers and keep freight moving.
You’ll learn about the best practices for loading and unloading containers quickly and safely, enabling you to accelerate cargo operations and increase efficiency for your port.
If you’d like to learn about protecting your port from various legal risks, check out this article I wrote on transload shipping agreements and crucial must-have elements.
In this article, we’ll discuss a guide to transloading containers and techniques to boost port productivity in 2024 and increase business revenue and efficiency overall.
Let’s get started.
What is container transloading?
Container transloading is the process of transferring cargo from one container to another, or even from a container directly onto different modes of transport.
You can do this with the aim of moving goods from the initial transportation, such as an ocean vessel, to a different form of transportation like trucks and railcars. It can also occur between two different ocean vessels or barges at sea.
Transloading containers is a great strategy for boosting shipping efficiency when you’re transporting loose freight that cannot be palletized or packaged.
That said, this form of transloading can also involve palletized or boxed goods too.
While container transloading typically occurs at a container yard or ocean port, it can also take place at different types of transloading facilities.
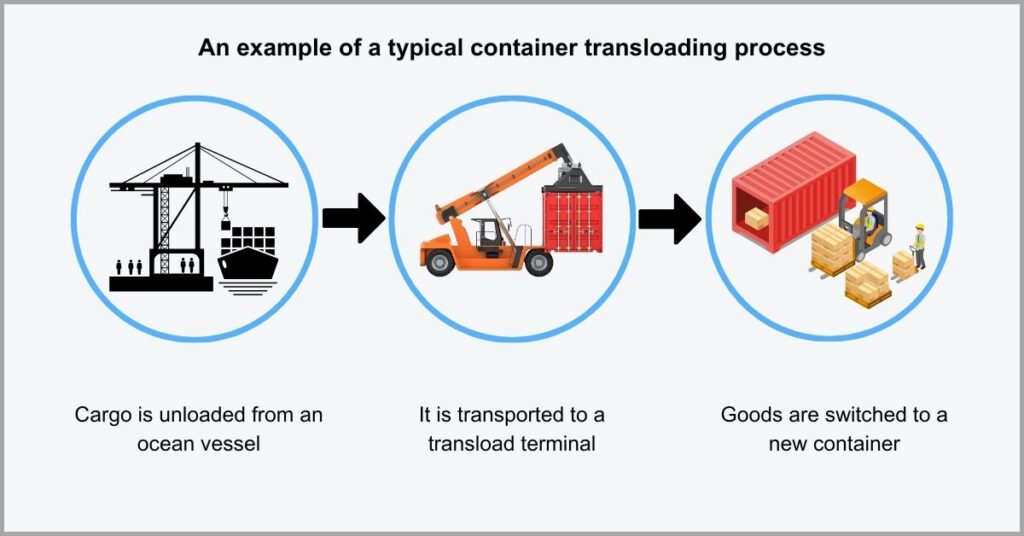
For instance, you can transload a container at a rail transloading yard.
This can be done to enable effective railcar switching, or to facilitate the transition of goods from a railcar onto a truck. The goal of transloading containers at this point could be to break apart the shipment into smaller consignments to enable last-mile deliveries.
However, transloading containers attracts unique inventory management needs. So I recommend using an excellent transload inventory management solution to keep track of goods you’re transloading in between containers.
Click here to book your free transloads.co demo to explore our inventory management features.
We’ll discuss how to pair our software with barcode scanners to improve inventory reconciliation and accelerate the process of transloading containers at your facility.
Container Transloading Equipment
a. Transloading container
So what is a transloading container?
A transloading container is simply a shipping container that you can load cargo into or unload cargo from when you’re transferring goods between different transport modes.
Proving an excellent solution for short term goods storage, a transloading container becomes a very cost-efficient solution for hauling bulk goods.
This equipment is also known as a transloading or intermodal shipping container, depending on whether or not the shipment is opened. If it is transferred as it is from the ship to a truck or railcar without opening, then it’s an intermodal container.
If you break open the container to transfer bulk goods inside to another container or directly to the new form of transportation, then it’s known as a transloading container.
b. Gantry crane
A gantry crane is a crucial piece of equipment.
It is a special machine that can hoist containers and transfer them from the shipping vessel and onto another place in the shipping yard or directly to a truck or railcar.
Without a gantry crane, you’d need to manually lift very heavy containers, which is time-consuming and labor intensive and also attracts huge safety risks.
This crucial transload shipping equipment solves these challenges by performing container transfers. A gantry crane often runs on its own dedicated rail tracks or bridge called a gantry, which enables great portability when you’re transloading containers.
Thanks to its controlled and very precise lifting system, it makes the process of transloading containers much more efficient and safer for both personnel & freight.
c. Reach stacker
What is a reach stacker and what does it do?
A reach stacker is a special vehicle that lifts and moves large shipping containers within a port, and has a heavy-duty boom that enables it to arrange containers accordingly.
Without a reach stacker to help you stack containers, your port can easily experience poor yard space utilization that results in congestion & delays.
This vehicle helps to avoid this by arranging containers in rows and stacking them up to five levels high.

Consequently, it’s a great tool to help you maximize storage space and keep freight moving in a very busy transload freight shipping terminal or shipping port.
Another great attribute of reach stackers is that they’re very versatile and can handle different sizes of containers. So they eliminate the need for additional equipment, therefore significantly eliminating extra costs for your transload terminal.
Transloading techniques to boost port productivity
1. Create a cargo loading plan
Proper planning is the key to success.
Before you move the container from the ocean vessel and into a loading dock or zone, you need to already have a strategy for how you want to transload the cargo.
Otherwise, failing to create a cargo loading plan can lead to poor loading and wasteful space utilization that ultimately inflates your operational costs.
A study by Container Xchange discovered a 20% increase in expenses for ports due to the renting of additional warehousing space for containers. One key contributor to this is inefficient storage.
So it’s essential to create a loading plan that enables you to make the most out of your existing space.
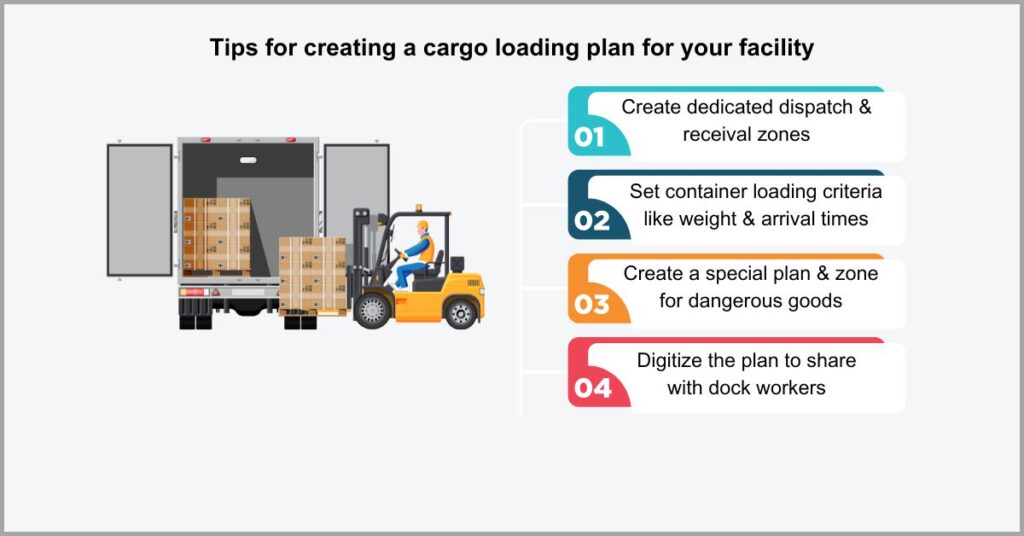
But how do you create a great cargo loading plan?
One way to go about it is to stack the goods according to weight parameters.
For example, you can start by floor loading the heavier items first into the new container, and then finish this off by layering lighter loads onto them.
This solves key transloading challenges by improving weight distribution to avoid the risk of the container tipping over during shipping. It also enables you to squeeze lighter cargo into gaps left by heavy goods to increase container space utilization.
For any empty space that still remains afterward, I recommend using dunnage bags to secure the cargo to prevent movement and damages during transit.
2. Leverage portable loading ramps
So what is a loading ramp?
A loading ramp is a sloped surface that enables you to move goods efficiently into an empty transload container. Alternatively, it also enables the smooth unloading of goods.
When you have very few loading docks compared to available trucks or containers, you can experience huge backlogs at your container port.
A study by Vector revealed that, for 39% of shipping yards, dock scheduling is the biggest challenge. In particular, some of the issues they’re experiencing is having limited loading docks compared to their transloading needs.
It’s therefore important to use container transloading strategies that take pressure away from your docks such as loading ramps.

This tool essentially allows you to create portable loading docks around your yard. It typically comes with wheels at the base, enabling you to move the loading ramp from one point to another depending on your transloading needs.
It gives you the freedom and flexibility to carry out loading and unloading processes from anywhere without the need to move the container to a dedicated loading dock. So it can make rail to truck transloading faster and much more efficient.
With a loading ramp, you can even drive forklifts into the container, pick up goods, and move them directly to a warehouse for storage or a waiting means of transportation.
3. Use container tracking technologies
Container yard visibility is critical to efficiency.
If you have poor visibility into your yard, it’s easy to lose track of the location of key assets, including not just containers but also machinery and personnel as well.
When you can’t locate containers and other resources on time, it also means that your transloading operations will be highly inefficient and therefore slow.
That said, you stand to improve dock throughput by up to 40% with real-time yard visibility, according to a study by FourKites. This means that you can work almost twice as fast with the right technologies in your workflow.
When that happens, productivity and profit margins increase for your facility.
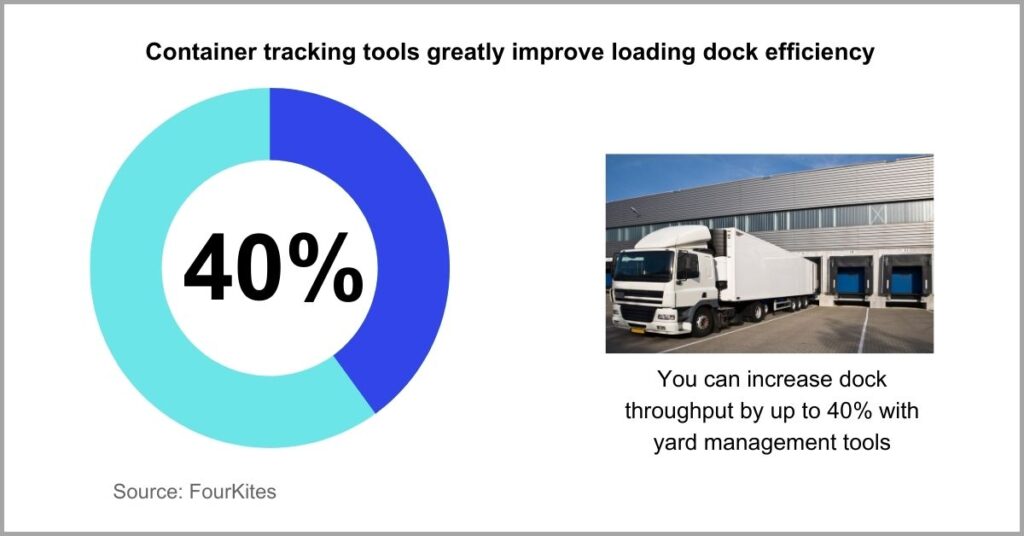
But how can you improve container yard visibility?
I recommend moving from manual container tracking solutions like Excel or pen and paper to digital and automated solutions that are much more efficient and effortless.
For example, you can turn to the best warehouse management tools such as our very own transloads.co. It gives you automated real-time tracking of yard assets such as railcars and containers, giving you data for making more informed decision-making.
With real-time yard visibility, you can implement a logical system of loading or unloading containers based on factors like arrival time or shipment urgency. This boosts your productivity and also reduces pick-up delays for your shipping port.
4. Take advantage of driver-assist loads
Port operations can get extremely busy sometimes.
During peak periods, you may receive a lot of containers that attract various transloading needs, but you may not have enough personnel to spare.
Furthermore, your port may also be grappling with a worker shortage, which can only aggravate port congestion, increasing the risk of missed timelines.
The average container throughput will increase to 988 TEUs (Twenty foot equivalent units) by 2027, up from 622 TEUs in 2012, according to a Statista survey. This is fueled by the rapid growth of international shipping.
So it’s safe to deduce that the demand for container transloading services will greatly increase and you need to accelerate operations to keep up.
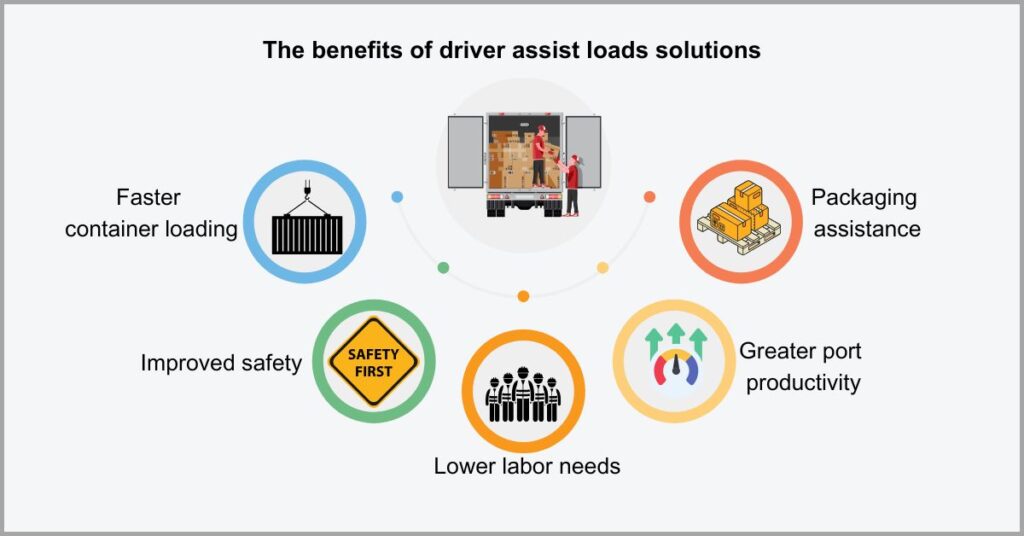
So what is a driver-assist load exactly?
A driver-assist load is a service that trucking companies may offer that essentially helps with container transloading to help plug any personnel gaps you have.
For example, if you request this service, the trucking company can have its own drivers and dedicated loaders assist with the loading or unloading process. Some may even go as far as helping you to palletize goods and store them in your warehouse.
Many of the best transloading companies use this tactic during peak periods.
It’s a strategy that can help you thrive during periods of high demand, without expanding your workforce or hiring temporary workers to cushion the increased work burden.
5. Adopt proactive container placement
How do you approach container storage in your yard?
If you wait for containers to arrive & then figure out the best places to put them, this can lead to the haphazard placement of containers, which makes transloading inefficient.
When container placement is poor, retrieval times increase for your dock workers, which negatively impacts your shipping port’s productivity.
An Oracle study showed that 81% of logistics leaders ranked improving productivity during logistics operations as “highly important” for success. It’s an understandable perspective given its impact on revenue.
With a proactive container placement strategy where you make arrangements for strategically storing containers before they arrive, you can greatly uplift productivity.
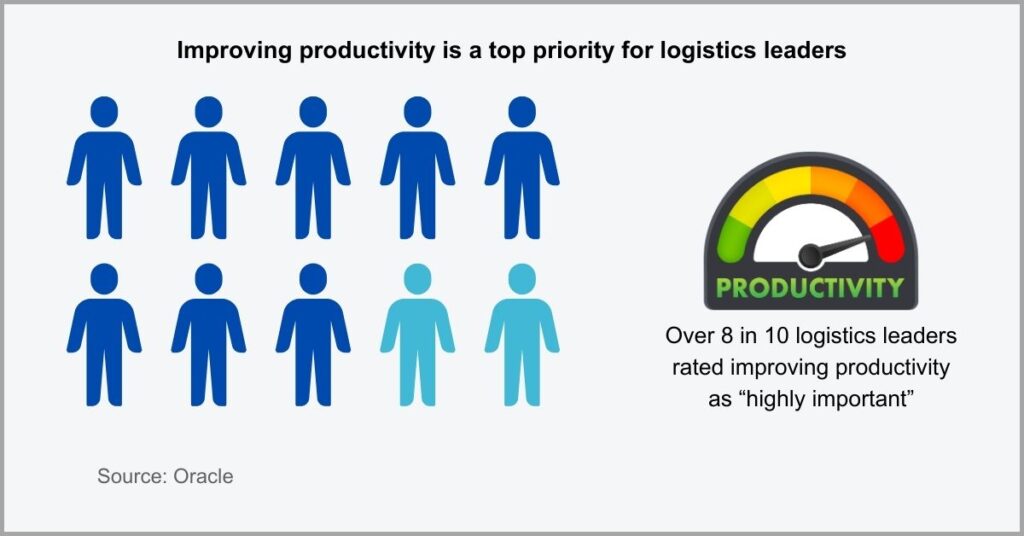
In order to execute this strategy, you’ll need to implement strategic zoning.
This entails splitting up your container yard into important sections such as inspection, cross-docking, dispatch and receiving areas, among others depending on your needs. Doing so will clamp down on unnecessary container handling and movements.
Speaking of optimizing your warehouse layout and operations, we also offer guidance to help you get the most out of your container yard.
Click here to get our premium support services to improve port efficiency.
With our assistance, you can optimize the layout of your facility and upskill workers in the best practices for transloading containers to improve port productivity and revenue.
Benefits of transloading containers
i. Enhanced freight capacity
International containers are usually smaller in size.
For instance, you’re limited to 40 foot or 20 foot options, whereas domestic containers in North America, and particularly the US, can reach lengths of up to 53 feet.
So shipping freight using only international maritime containers is unideal because it significantly limits freight capacity, which increases shipping costs.
A survey by Parcel showed that 37% of international shippers struggle with high cross-border shipping expenses. This made it the second top-most obstacle overall, but it’s a challenge that you can easily mitigate with transloading to improve shipping profits.
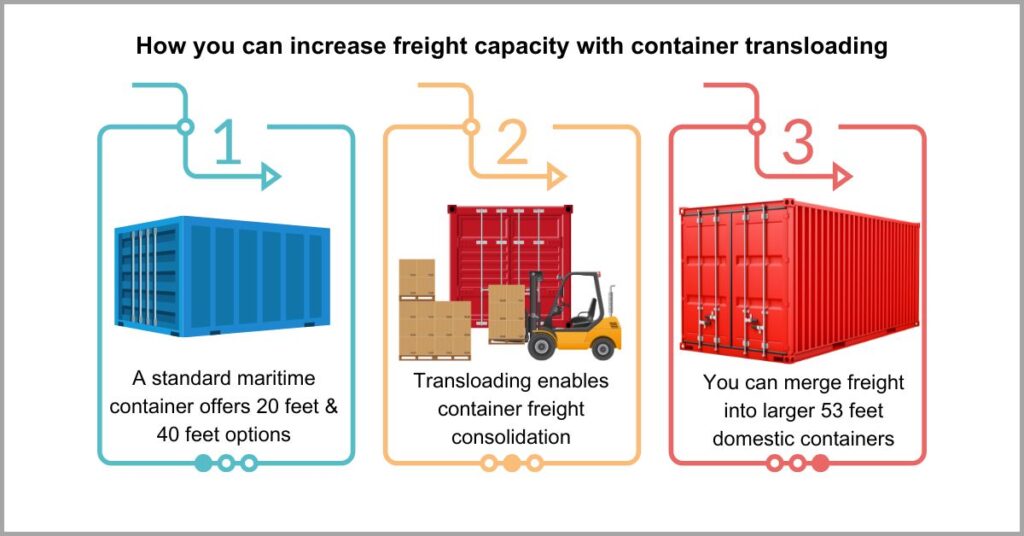
Container transloading breaks the freight limitations of maritime containers by enabling you to transition to higher capacity domestic containers to complete freight shipping.
It’s a popular trend during transloading and intermodal shipping operations, in particular, because it lowers expenses for shippers and carriers by enabling freight consolidation.
For your port, on the other hand, you can also minimize your cargo handling needs.
When this happens, dock workers become more productive and efficient, therefore decreasing turning around times for cargo operations to boost your profitability.
Additionally, it helps to reduce the number of containers you keep on site by packing cargo into larger storage units, which greatly improves space utilization as well.
ii. Improved weight compliance
Are there weight restrictions you need to observe?
While the goal of transloading containers is to pack a lot of cargo into a single container, this may not always be possible if there are weight restrictions you need to consider.
For example, some states have lower weight limits than others, and shipments may arrive in international containers that exceed these requirements.
A study by SCMR showed that 64% of logistics companies increased costs to over penalties from regulatory violations. Some of these infringements centered around failing to observe weight limits and abide by various environmental requirements.
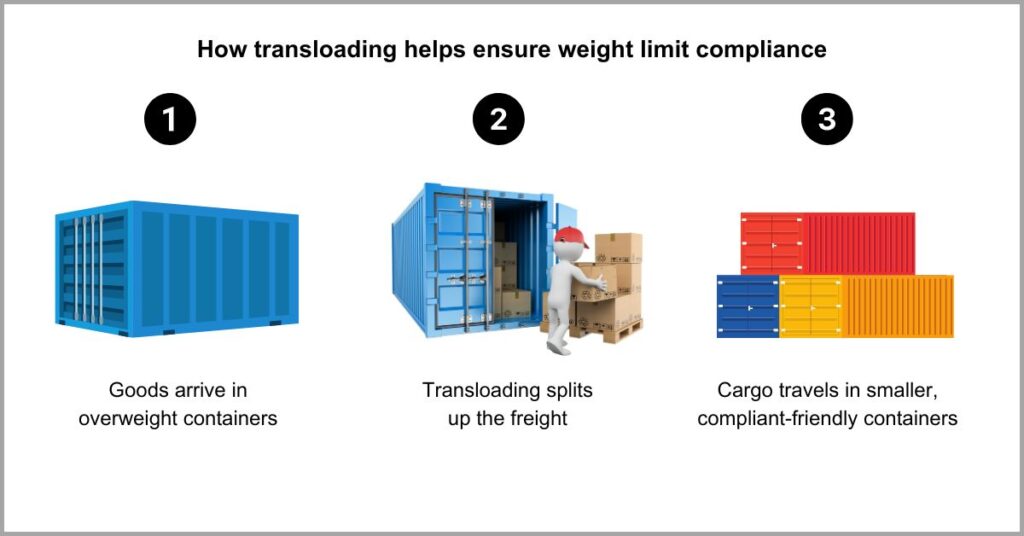
With container transloading, however, you can improve compliance particularly with regards to regulations about weight limits in certain states or regions.
While you can always obtain a special permit to move overweight freight, it can be a complicated and lengthy process that also attracts additional costs since you’ll also need to use specialized truckers and equipment.
If the consignment is going to be shipping through a jurisdiction with weight limits, you can implore transloading and transshipment strategies to redistribute the goods.
So you can easily unload overweight cargo from one container and distribute it into several containers so that each unit stays under the required weight limit.
iii. Palletization of goods
Goods in overseas containers are often unpalletized.
It’s a strategy that allows the floor loading of freight as loose goods, which enables your overseas shipper to pack as much cargo into the container as possible.
However, the non-palletization of goods makes them dependent on moving through containerization, which is unideal given prevailing container shortages.
A survey by the ACC revealed that 76% of ports are experiencing huge container shortages or imbalances. Through palletization and other packing strategies, transloading reduces the need to move goods as containerized freight.
This helps keep freight moving even during instances of container outages.
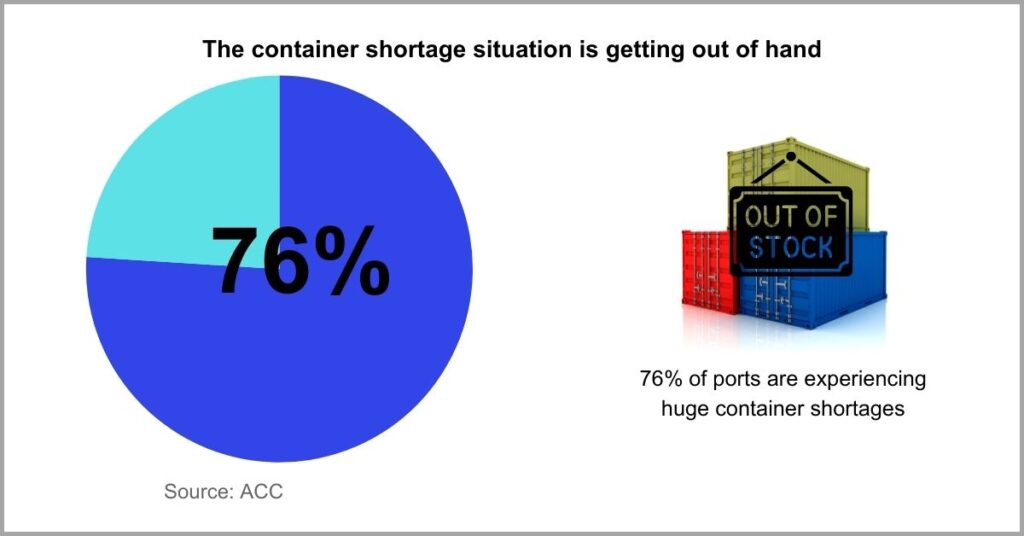
Palletization is one of the most vital warehouse and logistics trends today, because it also enables you to meet unique shipper needs. For example, it allows you to deconsolidate freight depending on the consignee’s different target locations.
It also makes the freight much easier to handle, with palletization improving the stackability of items, making them easier to sort and store inside transload containers.
What’s more, you can also lower your physical labor needs significantly by palletizing goods during transloading. So instead of transferring cargo as loose freight such as boxes, you move huge bulk shipments in pallets in one go using a forklift truck.
Conclusion
Slow cargo operations can be devastating.
They aggravate port congestion and add to long transit times for shippers.
With prolonged port delays and congestion, instances of blank sailing, where shippers skip your port in favor of more efficient facilities, can increase.
Unfortunately, only 19% of companies admitted that port-related delays are improving in 2024, according to a study by ACC. So, in other words, the majority of shippers believe these challenges won’t let up or will get worse.
If you’d like to reduce port congestion, the techniques we’ve covered for transloading containers we’ll help you decrease turnaround time to eliminate pileups. That said, leveraging the best transload management software also helps lower port delays.
Click here to book your free transloads.co demo to learn more about our tool.
You’ll learn how to use container tracking controls to optimize storage and also explore features for managing dock workers centrally to increase port productivity & throughput.