10 Essential Warehouse Management Software Features to Look Out For in 2024
Searching for a great warehouse management tool?
It’s important to choose the right warehouse software as it affects profitability.
If your warehouse management solution lacks key features like automation, for example, your labor needs will increase, thereby inflating your wage bill.
A survey by MMH revealed that 59% of warehouses plan to invest more in automation. This was because of labor shortages and time-sapping manual tasks.
With a solution that has the right warehouse management software features, you can automate various tasks in your workflow. This will help minimize your labor needs, reduce your operational costs and increase your margins .
From inventory tracking to order management, the right tool will reduce the time and effort that goes into iterative warehousing tasks to improve your productivity.
In this article, we’ll discuss essential warehouse management software features to look out for in 2024 to help you increase efficiency and grow your bottom line.
Let’s get started.
1. Inventory management
How do you track inventory in your warehouse?
If you rely on pen and paper or spreadsheets to stay on top of inventory levels, then you may know the pain of inaccurate manual input and the lack of real-time visibility over inventory assets.
In addition, manual inventory tracking solutions lack scalability and your inventory management processes will get very complex as your needs grow.
A survey by Hopstack revealed that, for 65% of warehouses, inventory tracking is the most important feature of a Warehouse Management Software (WMS). That’s because of how inventory management can be very hectic when you do it manually.
So the warehouse management software you go with should have inventory features that streamline and optimize inventory tracking to increase efficiency.
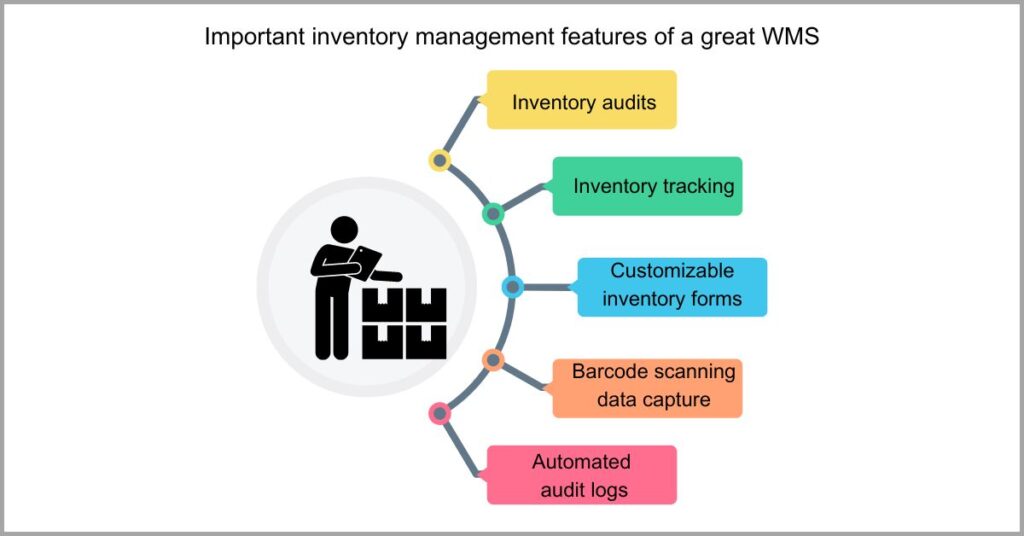
With automated inventory tracking and customizable inventory forms, for example, things become much easier for your warehouse.
You can bring up stock levels in an instance on a centralized dashboard without the legwork, thereby getting an accurate perception of the state of your inventory at all times. This enables you to make informed decisions about restocking.
I also recommend going for solutions with barcode scanning technology to automatically capture inventory data and reduce the risk of manual input errors.
Moreover, other warehouse software features to prioritize are inventory audits.
This will help you identify slow-moving inventory and minimize your overhead costs by optimizing your stock levels. In addition, it’ll also make it easier to identify inventory shrinkage and perform demand forecasting more accurately.
2. Workforce management
Proper worker coordination is paramount for success.
If teamwork is poor and everyone is not quite clear on what they need to do and when, team efficiency takes a nosedive, which can lead to delayed orders and lost customers.
Furthermore, work allocation can also be poor if you lack a system for managing and balancing workloads, leading to burnout and high employee turnover.
A study by UIC uncovered that up to 60% of warehouse workers suffer burnout due to the demanding nature of the jobs. As a result, injury incidents increased due to poor attentiveness while their efficiency at work also dropped.
This emphasizes the need to consider warehouse management software features that can help you allocate work more strategically and efficiently.
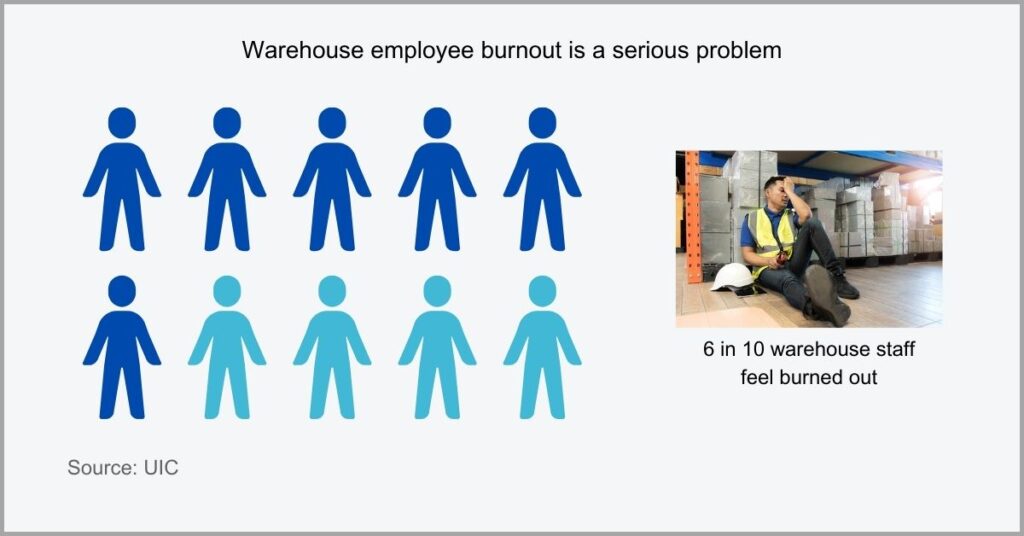
So what workforce management features are important?
One of the very basic capabilities you should prioritize is the ability to allocate tasks, optimize schedules and track general workplace performance for warehouse workers.
It should enable you to monitor important productivity KPIs for your business, such as picking accuracy and orders fulfilled, among others, which enables you to identify productivity bottlenecks and improve staff performances.
With some of the best inventory management systems, you may also get demand forecasting features. These estimate workloads for the day, enabling you to plan your staffing needs better to optimize labor expenses and reduce work overloads.
Other software may also provide warehouse worker on-boarding and offboarding capabilities which can help you reduce your time to hire and improve quality of hire.
3. Electronic invoicing
Does the WMS have electronic invoicing features?
Oftentimes, you may need a separate solution for your warehouse management needs and a different software to handle invoicing. But this is very unideal because it attracts a lot of financial reconciliation work that increases the risk of human error.
When invoices are inaccurate, your warehouse can experience increased cases of delayed payments, order cancellations and even legal disputes.
For transportation and logistics businesses, 46% of invoices are paid late, according to a study by Upflow. One of the key reasons for these delays are invoicing errors, like missing payment instructions, wrong recipients and incorrect payment amounts.
This is why you need to prioritize warehouse management software features like e-invoices which can help you lower the risk of such invoicing mistakes.
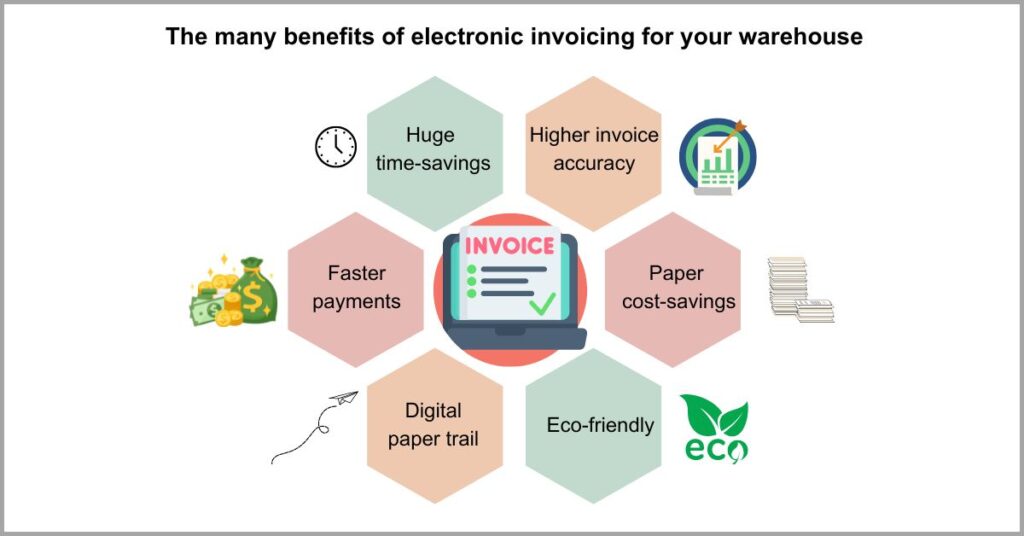
Our software, transloads.co, is an excellent choice for your e-invoicing needs.
You can enjoy the benefits of a great transloading software such as more accurate invoices with our e-invoicing functions. This lets you create bulk and individual invoices to meet the unique needs of all your customers.
If you’re a transloading warehouse, you’ll get even more use out of our solution. It lets you set rates for indoor and outdoor handling, and add custom and incidental charges. This helps ensure more accurate remuneration for your business.
What’s more, transloads.co also integrates seamlessly with QuickBooks.
This allows you to export data between both platforms with ease, thereby enabling you to reconcile financial reports using inventory data much more accurately and effortlessly.
4. Security controls
Your WMS may handle sensitive information.
From customer’s personally identifiable information to confidential employee records, you may directly or indirectly through integrations with your CRM or HRM system, process sensitive data that’s usually a prime target for hackers.
When your WMS has weak security controls, your business becomes vulnerable to data breaches that lead to loss of intellectual property and law suits.
Cyber security is a huge concern today with 78% of businesses citing third-party vendors like WMS providers as a huge security risk, according to a BlueVoyant study. Many of these companies are planning to increase their security budgets as a result.
It’s consequently important to go with a warehouse management software with robust security controls because this will help keep your data safe and save you money.
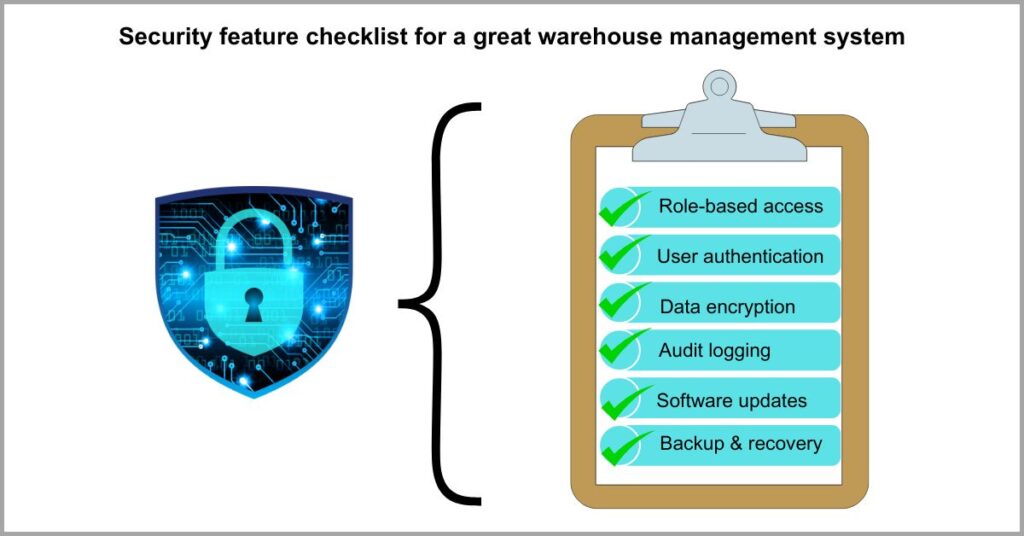
So what security features should you look for in your WMS?
The first line of defense of any great system is typically access control and authentication. Access control gives you the power to define role-based access, which reduces the risk of data tampering as well as unauthorized access.
When you’re choosing a warehouse management system, you should also determine if it leverages the latest and most effective data encryption technologies.
This is key to helping you protect financial transactions and supplier details by ensuring that even if a hacker intercepts transmitted or stored data, they cannot read the information and so it’s useless to them.
With a robust and secure WMS, you can mitigate cyber security risks to protect warehouse assets, customers and your business’s industry reputation.
5. Customer portal
A customer portal is also a very important feature.
Without it, what happens behind the scenes from your customer’s point of view is shrouded in mystery because they can’t readily access cargo data in real time, therefore creating very limited shipment visibility that breeds mistrust.
On top of that, disjointed conversations resulting from traditional communication strategies can also lead to misunderstandings and delayed cargo releases.
A survey by Tive revealed that 77% of supply chain leaders said real-time shipment visibility is a must-have feature. This is because of the growing demand for shipment traceability from customers, who would choose a competitor because of it.
Consequently, customer portals are among the top warehouse management software features you should prioritize as not doing so can lead to lost sales.
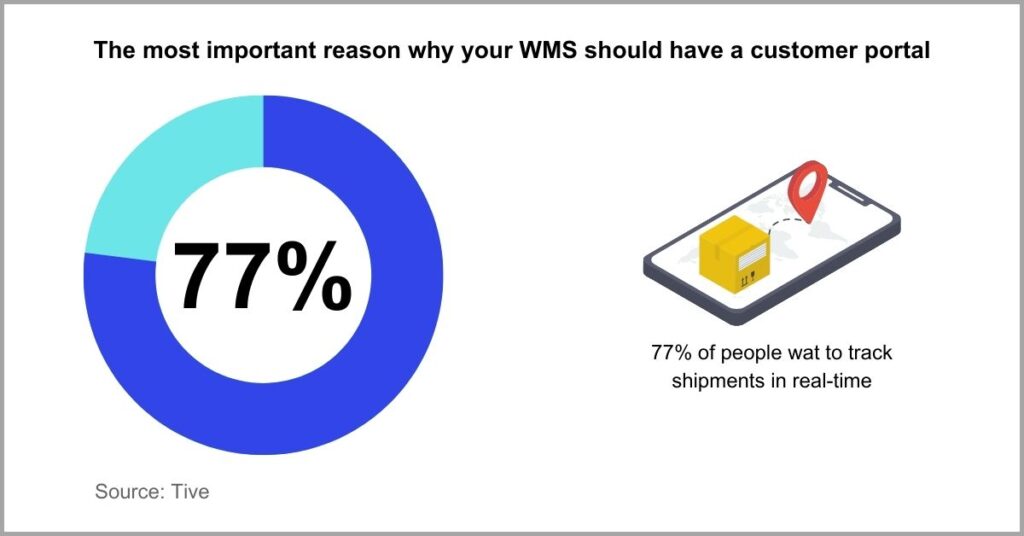
So what should the customer portal be able to do?
At the very least, it should provide real-time shipment tracking to give clients up-to-the-minute updates about their cargo to free up your team for other tasks. This will also help customers feel valued and appreciated, which raises satisfaction and loyalty.
If you’re a transload shipping business, customer portals can also come in handy for many other purposes.
For instance, they enable your clients to submit unique requests about how they want you to store, palletize or ship their cargo. This helps ensure fewer disputes and reduce the risk of cargo rejection
With some customer portals, you can obtain quote requests faster to streamline your quoting processes, which helps you increase efficiency and land more clients.
6. Order management
It’s easy to lose sight and control of orders.
This risk greatly increases more so if your warehouse receives orders from multiple channels and works with multiple shipping companies and picking and packing entities among other partners in your supply chain.
When order management is ineffective, you may ship incorrect products or experience delayed shipments that increase customer dissatisfaction.
In fact, PowerReviews discovered that 79% of product returns occur because an item arrived late or had some sort of defect or damage. So this means that, most of the time, returns happen due to the fault of the retailer rather than the customer.
One of the biggest reasons for these mistakes is poor order visibility, which underscores the importance of a WMS that has the right order management features.
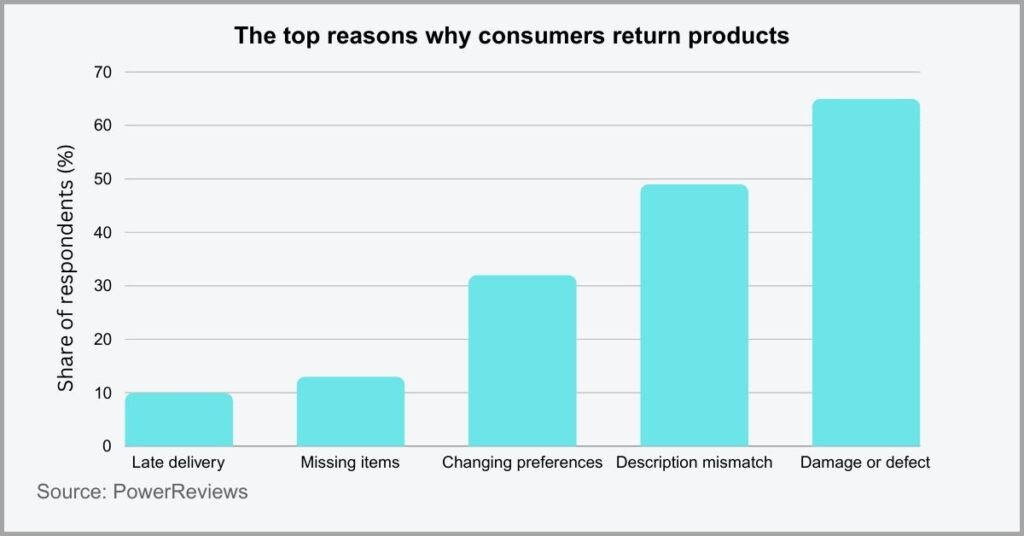
But what are the key functions to look for in order management?
First, I recommend warehouse yard management software that can centralize order management, because this unified oversight makes your workflow more efficient.
With this feature, you can track and receive orders from multiple channels more effortlessly to ensure none slips through the cracks.
This will also help you fulfill order requests faster and more accurately, which in turn enables you to meet and even exceed customer expectations. When this happens, customers stay loyal and your brand gets more repeat business.
Furthermore, the right tool should offer customizable automation rules for common tasks such as order tracking, dispatch updates, and order report generation, among others, to help improve productivity for your warehouse.
7. Reverse logistics
Does it have return management capabilities?
While unfortunate and highly undesirable, returns and reverse logistics are an unavoidable reality of running any warehouse. This can arise from customers changing their minds, mixups in deliveries or shipment of defective items, among other reasons.
Notably, the expenses associated with handling returns can quickly skyrocket if your warehouse lacks a strategy for efficient reverse logistics management.
Proper return handling is very important given that 95% of customers say that they would never do business again with a brand after experiencing a poor returns process. So reverse logistics is a make or break affair for your warehouse.
Consequently, it’s important that your warehouse management software helps you improve your returns processes so that you don’t lose customers and revenue.
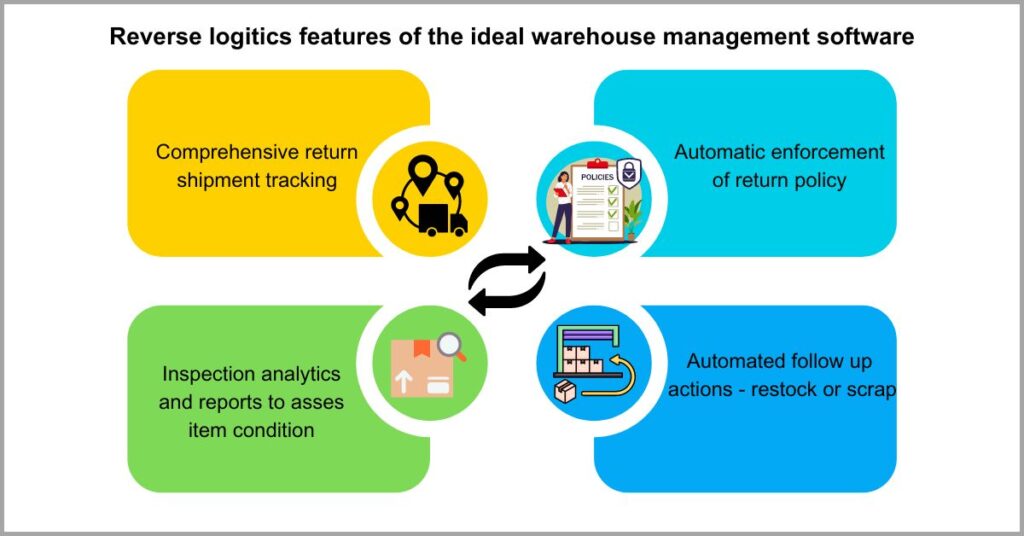
An important function to scrutinize here is real-time tracking.
As a bare minimum, your WMS should be able to track return shipments to help eliminate the risk of items being lost during transit back to your warehouse.
It’s also crucial that the warehouse inventory management solutions you’re considering can enforce return policies automatically to help improve operational efficiency, enhance customer satisfaction and reduce the risk of product return fraud.
Other key warehouse management software features to consider are inspection analytics with follow-up action suggestions such as restocking or scraping.
This should also include the ability to log the reason for the return and automatically execute a return action, like exchanging the item or reimbursing the customer based on inspection findings to help improve return process efficiency and transparency.
8. Integration features
What business technologies do you presently rely on?
As a warehouse with diverse needs, you may depend on a variety of software solutions to keep your operations ticking. This can include platforms such as your ERP, accounting software and CRM, among others.
If your warehouse management software doesn’t readily integrate with your underlying applications, this can create data silos that hinder productivity.
In fact, approximately 22% of employees spend over 20 hours a week searching for data in fragmented information systems. This is fueled primarily by disparate technologies that have no way of communicating with each other.
This is a mind-blowing statistic which shows the huge productivity loss of data silos, and emphasizes the need for a WMS that’s compatible with your existing technologies.
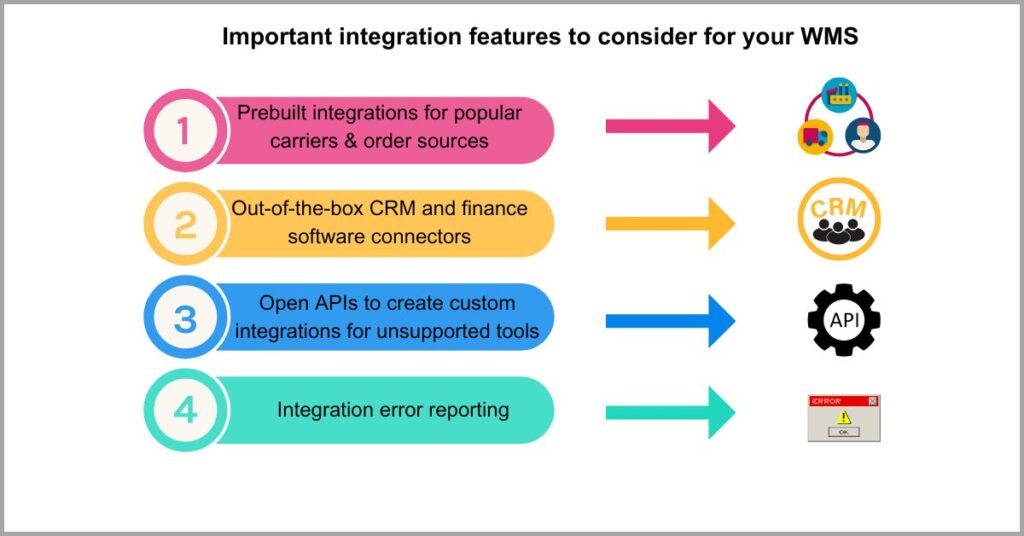
In terms of what you should be looking for with regard to integration features, I recommend going for a tool with prebuilt integration options for your CRM, ERP, or accounting platform.
This will help you hit the ground running and lower downtime.
When you’re choosing a transload management solution, you should also consider whether it offers open APIs if pre-built connectors aren’t offered.
These custom APIs will enable you to create integration options in cases where your underlying solutions are not readily available to help break potential data silos.
In doing so, integration features will help you unite data across disparate systems.
You’ll therefore get end-to-end visibility over warehouse operations by centralizing information, and this also increases your productivity and efficiency.
9. Location management
Warehouse space is one of your most valuable resources.
It determines how much inventory you can keep on hand and directly influences your business’s bottom line as waste may necessitate the need to rent out more space.
When warehouse space is not efficiently utilized, this can also increase your cost per order and subsequently reduce profit margins for your business.
It’s very alarming to note that 36% of warehouses said that insufficient inventory space is one of the biggest problems, according to a Statista survey. As a result, this led to overcrowding, which decreased efficiency and attracted huge safety risks.
So it’s important to prioritize warehouse management software features like location management to help maximize space utilization and improve warehouse profitability.
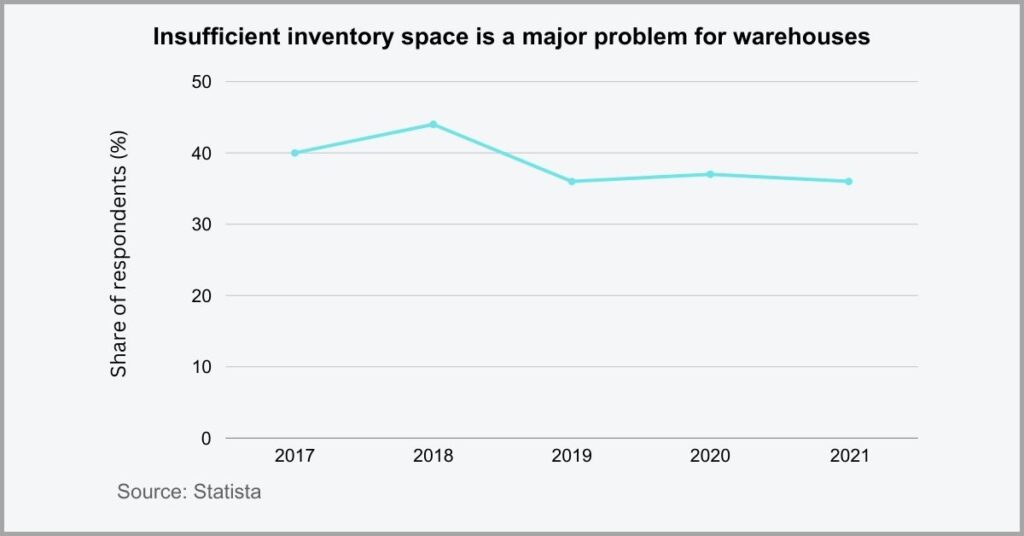
But what location management capabilities are important?
Well, the best warehouse management software should give you a virtual warehouse map. They should show zones, and even individual cargo and item locations in real-time, down to comprehensive details about stacking and weight.
With this data, you can optimize your inventory to ensure proper stacking and minimize waste to squeeze more value out of your existing floor space.
These depictions of inventory locations may also help you track down items in your warehouse down to the shelf, column or aisle, to make order retrieval fast and efficient to accelerate your fulfillment processes.
If you run multiple warehouses, it should also offer a centralized hub for managing these different locations in one place to provide real-time oversight of all your operations.
10. Cloud computing
Is the WMS cloud-based or on-premise?
An on-premise solution gives you greater resilience over disruptions but this comes at a huge sacrifice in terms of scalability. As your warehousing needs grow, it will be difficult to adapt it to your workflow, and you may abandon it altogether.
In addition, lack of cloud-based capabilities in your warehouse management software can massively hinder information sharing and collaboration.
A survey by Statista revealed that 44% of businesses who embraced computing technologies improved employee experiences and collaboration. This is largely because of streamlined communication and remote access to information.
With a cloud-based warehouse management system, you can therefore significantly improve team productivity to accelerate order fulfillment, encourage innovation and enhance employee satisfaction as well for your warehouse.
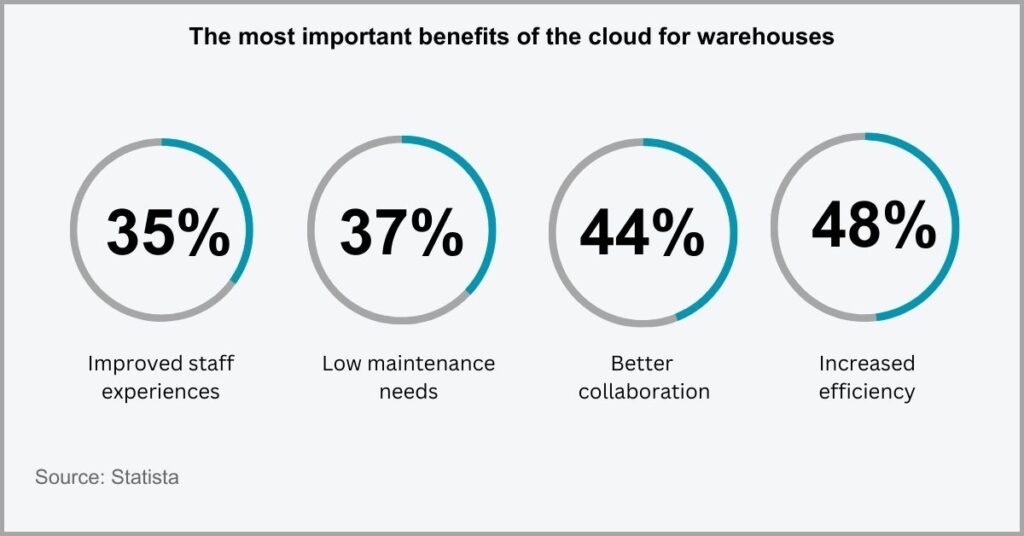
In terms of specific cloud computing capabilities to look for, I recommend going with a platform that enables cloud document storage.
This will allow you to store packing lists, bills of lading and other documents in the cloud, enabling warehouse workers to access important details and shipping instructions from their mobile devices to help improve order picking accuracy.
In addition, other benefits of transload warehouse software that are cloud-based is improved disaster recovery.
While you can easily lose all your data and have to start from scratch with an on-premise solution, a cloud-based WMS automatically creates data backups and restore points to help you bounce back quickly from data loss events.
So it helps improve disaster recovery and minimize business-crippling disruptions for your warehouse to reduce the risk of lost sales.
Conclusion
Your warehouse has its compliance obligations.
From worker safety laws to legislation requiring supply chain traceability, there are several compliance requirements to consider.
If you have poor visibility over warehousing processes, compliance bottlenecks grow unchecked, attracting the risk of penalties for your business.
A survey by Reslinc revealed that 50% of supply chain professionals rate identifying compliance risk as a top challenge. One of the driving factors behind this struggle is poor process visibility.
So it’s important to choose a solution that has the right warehouse management software features to help you improve compliance. Overall, I recommend transloads.co which enhances warehouse visibility to help you uncover compliance risks.
Click here to start your free transloads.co trial for a solution that ticks all the right boxes for your transloading warehouse.
With our software, you’ll get robust inventory management to improve inventory accuracy and insightful business reports that help improve productivity and efficiency.